آشنایی با تجهیزات ثابت و دوار و کاربرد آنها
تجهیزات ثابت که گاهی به عنوان تجهیزات استاتیک نیز شناخته می شود، اصطلاحی است که عموماً برای توصیف تجهیزات غیر متحرک در صنایع نفت و گاز و فرآیند استفاده می شود. برخی از نمونهها شامل مواردی مانند مخازن تحت فشار، مبدلهای حرارتی، لولهکشی، مخازن ذخیرهسازی، شیرها، دستگاههای کاهش فشار، بویلرها، کورهها و هیترها و سازهها هستند. از سوی دیگر، تجهیزاتی مانند پمپ ها، کمپرسورها، توربین ها، تجهیزات الکتریکی یا ابزار دقیق (I&E) تجهیزات دوار نامیده می شوند حتی اگر ثابت باشند. در این مطلب با انواعی از تجهیزات ثابت و دوار آشنا خوهایم شد.
تجهیزات ثابت
تجهیزات ثابت یا استاتیک یک اصطلاح کلی برای توصیف تجهیزات غیر متحرک در صنایع نفت، گاز و فرآیند است. برخی از نمونه ها شامل مخازن تحت فشار، مبدل های حرارتی، مخازن ذخیره سازی، بویلرها، کوره ها و بخاری ها هستند. تجهیزات ثابت شامل مواردی مانند پمپ ها، کمپرسورها، توربین ها، تجهیزات الکتریکی یا ابزار دقیق نمی شود، حتی اگر معمولاً حرکت نمی کنند.
خطرات مرتبط با تجهیزات ثابت در مقایسه با سایر انواع تجهیزات به دلیل تعداد زیاد قطعات تجهیزات و مقدار سیال ذخیره شده بیشتر است. در یک پالایشگاه یا تأسیسات پتروشیمی معمولی، بخش قابل توجهی از هزینه تعمیرات و رویدادها یا خرابی های قابلیت اطمینان مربوط به تجهیزات ثابت است. درصد قابل توجهی از حوادث صنعتی که منجر به صدمات یا از دست دادن دارایی شده است نیز با تجهیزات ثابت مرتبط بوده است.
تجهیزات ثابت اغلب در معرض شرایط عملیاتی نسبتاً شدید و مکانیسمهای آسیب متفاوتی قرار میگیرند. در بیشتر موارد، آسیب آنی نیست و میزان خسارت خطی نیست. یک مثال خوب از این آسیب خوردگی تحت عایق (CUI) است که می تواند در طول زمان ایجاد شود، اما بلافاصله آشکار نیست.
برخلاف سایر انواع تجهیزات، تجهیزات ثابت سنسورهای پیچیده ای ندارند که بتوان از آنها برای نظارت بر خوردگی و آسیب در زمان واقعی استفاده کرد. به همین دلیل تجهیزات ثابت باید با بازرسی در فواصل زمانی ثابت کنترل شوند. به همین دلیل بسیار مهم است که یک طرح قابلیت اطمینان برای همه تجهیزات ثابت وجود داشته باشد.
تجهیزات ثابت جزء ضروری هر کارخانه و تأسیساتی است، بنابراین حفظ آن در شرایط خوب مهم است.
واحدهای کوکر
واحدهای کوکر یا کوکرها، واحدهای فرآوری پالایشگاه نفت هستند که باقیمانده نفت و باقیماندههای فرآیند پس از تقطیر خام اولیه را به محصولات با ارزش بالاتر و کک نفتی، مادهای شبیه زغال سنگ که به عنوان ورودی سوخت یا مواد خام تولیدی در انواع مختلف استفاده میشود، تبدیل میکنند. در طی فرآیند کک سازی، روغن باقیمانده از واحد تقطیر خلاء به راکتورهای عمودی بزرگ که به نام درام کک شناخته می شوند، منتقل می شود. در آنجا، تحت حرارت و فشار بالا در فرآیندی به نام ترک حرارتی قرار میگیرد تا بخارات سبکتر از جمله گازهای هیدروکربنی، نفتا و روغنهای گاز سبک و سنگین (که از بالای درام کک برای تصفیه بیشتر خارج میشوند) از بخار جدا شود. کک نفتی جامد شده این کک در درام انباشته میشود و پس از پر شدن، درام باید از حالت آفلاین خارج شود و با استفاده از دستگاههای برش آب فشار بالا برای احیا یا ذخیرهسازی، کک را خارج کنید.
دو نوع اصلی از واحدهای کوکر مورد استفاده در پالایش نفت وجود دارد: واحدهای کوکر تاخیری (DCU) و واحدهای کوکر سیال. از بین این دو، واحد کوکر تاخیری (DCU) بسیار رایج ترین است و شامل دو یا چند درام است که پشت سر هم کار می کنند. هنگامی که یک درام آفلاین می شود، تولید به سادگی به درام بعدی منتقل می شود. این به یک مرکز اجازه میدهد تا به طور مداوم یک کوکر آنلاین داشته باشد و از توقف غیرضروری جلوگیری کند. در یک کک سیال، خوراک از طریق همان فرآیند ترک حرارتی انجام می شود، اما کک تشکیل شده به عنوان یک جامد سیال به یک بخاری جداگانه منتقل می شود، جایی که مقداری از آن سوزانده می شود تا گرمای لازم برای کوکر برای ادامه تبدیل روغن باقیمانده به آن فراهم شود. گازها، مایعات مقطر و کک. کک سازی سیال می تواند بازده تقطیر بالاتر و بازده کک کمتری نسبت به کک سازی تاخیری ایجاد کند.
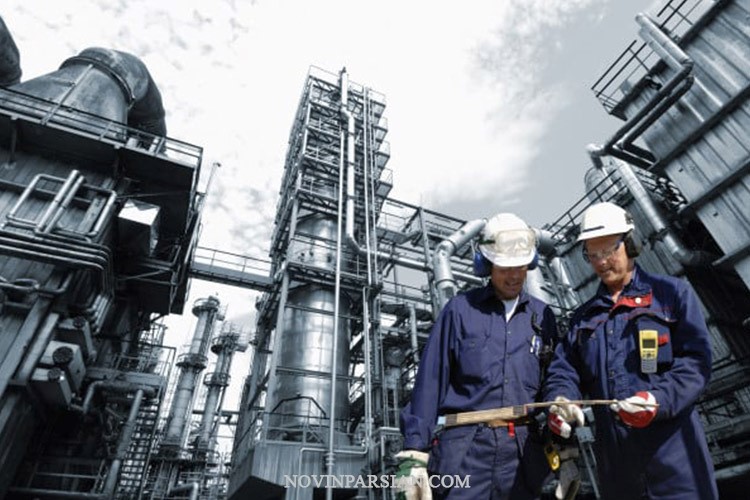
برج های خنک کننده
برجهای خنککننده دستگاههای دفع گرما هستند که گرمای اتلاف را از طریق خنککردن جریان آب تا دمای پایینتر به اتمسفر استخراج میکنند. کاربردهای رایج برای برج های خنک کننده تامین آب خنک برای صنایع مختلف مانند تهویه مطبوع، ذوب و … است.
اصطلاح عمومی “برج خنک کننده” برای توصیف تجهیزات دفع حرارت مستقیم (مدار باز) و غیر مستقیم (مدار بسته) استفاده می شود. برج خنککننده مستقیم یا مدار باز ساختاری محصور با وسایل داخلی برای توزیع آب گرمی که به آن وارد میشود روی یک بستهبندی هزارتو مانند است. پرکننده ممکن است از چندین سطح عمودی و خیس تشکیل شده باشد که لایه نازکی از آب روی آنها پخش می شود. یک برج خنک کننده غیرمستقیم یا مدار بسته شامل هیچ تماس مستقیمی با هوا و سیال، معمولاً آب یا مخلوط گلیکول، در حال خنک شدن نیست.
در یک برج خنک کننده با جریان مخالف، هوا از میان بسته های پر یا لوله، برخلاف حرکت رو به پایین آب، به سمت بالا حرکت می کند. در یک برج خنک کننده با جریان متقاطع، هوا به صورت افقی از میان پر کننده حرکت می کند و آب به سمت پایین حرکت می کند. برج های خنک کننده نیز با وسیله ای که هوا به وسیله آن جابجا می شود مشخص می شوند. از آنجایی که تبخیر از آب خالص تشکیل شده است، غلظت مواد معدنی محلول و سایر جامدات در آب در گردش افزایش می یابد، مگر اینکه ابزاری برای کنترل جامدات محلول، مانند دمیدن، فراهم شود. مقداری از آب نیز توسط قطراتی که با هوای خروجی (دریفت) خارج می شوند، از دست می رود.
واحد تقطیر خام (CDU)
در پالایش نفت، واحد تقطیر خام (CDU) که به عنوان واحد تقطیر جوی نیز شناخته می شود، معمولاً اولین تجهیزات پردازشی است که نفت خام از طریق آن تغذیه می شود. نفت خام از مخلوطی از هیدروکربنها تشکیل شده است و فرآیند تقطیر این نفت خام را به دستههای گستردهای از هیدروکربنهای تشکیلدهنده آن یا «کسری» تقسیم میکند، که بهعنوان ماده اولیه برای تمام واحدهای فرآوری دیگر در پالایشگاه عمل میکند.
همانطور که نفت به واحد تقطیر خام وارد می شود، اولین چیزی که اتفاق می افتد این است که نفت خام تا دمای بین 215 درجه فارنهایت تا 280 درجه فارنهایت (100 درجه سانتیگراد تا 137 درجه سانتیگراد) گرم می شود. این اجازه می دهد تا نمک هایی که می توانند برای برخی تجهیزات مضر و خورنده باشند در نمک زدایی حذف شوند. نفت خام نمک زدایی شده بیشتر تا دمای 750 درجه فارنهایت (400 درجه سانتیگراد) گرم می شود زیرا به برج تقطیر جوی وارد می شود که در آن بخارات و مایعات بر اساس دماهای مختلف جوش / متراکم جدا می شوند. در دماهای بالاتر از 750 درجه فارنهایت (400 درجه سانتیگراد)، روغن از نظر حرارتی ترک میخورد یا از هم میشکند که فرآیند تقطیر را مختل میکند.
هیدروکربن های سبک تر در نقاط بالاتر برج تقطیر متراکم می شوند، در حالی که هیدروکربن های سنگین تر در برج کمتر متراکم می شوند. این هیدروکربن ها (به عنوان مثال، نفتا، نفت سفید، گازوئیل و نفت گاز) سپس از طریق جریان های مختلف در ارتفاعات مختلف به خارج از برج منتقل می شوند و برای پردازش یا ترکیب بیشتر به واحدهای دیگر در پالایشگاه فرستاده می شوند. سنگین ترین هیدروکربن هایی که تبخیر نمی شوند از پایین برج اتمسفر کشیده می شوند و به واحد تقطیر خلاء فرستاده می شوند تا بیشتر تصفیه شوند.
هواگیر
هواگیرها دستگاه هایی هستند که برای حذف گازهای محلول، عمدتاً اکسیژن و همچنین دی اکسید کربن، از آب تغذیه بویلرها از طریق فرآیندی به نام هوازدایی استفاده می شوند. هواگیرها ضروری هستند زیرا اکسیژن محلول می تواند باعث خوردگی آب تغذیه دیگ بخار (BFW) شود که در صورت عدم کنترل می تواند به طور باورنکردنی برای دیگ مضر باشد. این نوع خوردگی عموماً به شکل حفره در قسمت جلویی دیگ، سیستم تصفیه، خطوط و پمپ های آب تغذیه و سیم پیچ های پیش گرم می باشد.
همچنین این فرآیند باعث گرم شدن بیشتر آب دیگ می شود که می تواند خطر شوک حرارتی در دیگ را کاهش دهد. فرآیند هوازدایی همچنین دمای آب را افزایش می دهد که به کاهش میزان سوخت مورد نیاز برای تبدیل آب تغذیه به بخار کمک می کند و در نتیجه راندمان دیگ بخار را بهبود می بخشد.
هوازدایی را می توان به یکی از چند روش مختلف انجام داد. روشهای اولیه هوازدایی، هواگیرهای نوع سینی و اسپری هستند.
در هر دو روش، فرآیند با وارد شدن آب به هواگیر شروع می شود. در هواگیرهای نوع سینی، آب به داخل محفظه جریان می یابد در حالی که بخار به طور همزمان به سمت بالا از محفظه از طریق آب جریان می یابد. این بخار آب را تا دمای اشباع خود گرم می کند و به آن اجازه می دهد تا اکسیژن محلول آب را قبل از خروج از هواگیر و به اتمسفر خارج کند.
روش نوع اسپری متفاوت است، زیرا، در حالی که آب هنوز به یک محفظه بخار تغذیه می شود، این کار از طریق اسپری انجام می شود، نه اینکه اجازه داده شود جریان یابد. این به همراه یک پیش گرمکن باعث می شود که آب تا دمای اشباع خود گرم شود به طوری که با پمپاژ بخار به داخل محفظه قادر است به راحتی آب اکسیژن محلول خود را از بین ببرد.
روش های دیگری نیز وجود دارد، مانند هوازدایی خلاء و کندانسورهای هوازدایی، اما این روش ها چندان رایج نیستند.
فلنج ها
فلنج ها برآمدگی های خارجی روی تیرها یا لوله ها هستند که به آنها اجازه می دهد به اشیاء دیگر متصل شوند. در صنایع فرآیندی و آموزشگاه فنی فلنج ها اغلب در زمینه خطوط لوله و لوله کشی مهم هستند. بخش های لوله می توانند در این فلنج ها به یکدیگر پیچ یا جوش داده شوند. امکان حمل و نقل، مونتاژ، نصب و/یا جداسازی آسان تر از زمانی که آنها به عنوان یک بخش بزرگ ساخته می شدند. با آسانتر کردن جداسازی آنها، فعالیتهای تعمیر و نگهداری، بازرسی و تمیز کردن را میتوان بدون تأثیر بر بخشهای بزرگی از سیستم لوله انجام داد.
برخی از رایج ترین انواع فلنج در صنعت عبارتند از فلنج های گردنی جوشی، فلنج های لغزنده، فلنج های جوشی سوکت، فلنج های مفصلی، فلنج های رزوه ای و فلنج های کور. آنها می توانند از تعدادی مواد مختلف مانند فولاد ضد زنگ، چدن، آلومینیوم، برنج، برنز یا پلاستیک و غیره ساخته شوند. معمولا مواد فلنج مانند خود لوله است.
ناحیه ای که دو لوله توسط فلنج به یکدیگر متصل می شوند به نام اتصال فلنجی شناخته می شود. این یک منطقه حیاتی برای مدیریت یکپارچگی یک سیستم لوله کشی است. نشت می تواند شروع تولید را به تعویق بیاندازد، باعث خاموش شدن برنامه ریزی نشده یا حوادث ایمنی قابل توجهی شود. همه اینها می تواند تأثیر قابل توجهی بر بودجه داشته باشد. به همین دلیل است که شیوه های موثر مدیریت یکپارچگی مشترک بسیار مهم است.
واحد تقطیر خلاء (VDU)
در پالایش نفت، واحد تقطیر خلاء (VDU) یک واحد فرآوری ثانویه است که روغنهای سنگینتر باقیمانده پس از عبور اولیه نفت خام از واحد تقطیر اتمسفر، که به عنوان واحد تقطیر خام (CDU) نیز شناخته میشود، را بیشتر تصفیه میکند.
در واحد تقطیر خلاء، روغنهای باقیمانده از CDU تحت خلاء با فشارهای بسیار پایینتری نسبت به CDU تقطیر میشوند. در این فشارهای پایینتر، نقطه جوش روغنهای باقیمانده به اندازهای کم است که محصولات سبکتر میتوانند بدون ترک خوردن تبخیر شوند و فرآیند تقطیر را مختل کنند.
تقطیرهای سنگین تولید شده در طی فرآیند تقطیر خلاء شامل نفت گاز سبک و نفت گاز سنگین است که سپس به واحدهای جداسازی و تبدیل پایین دست فرستاده میشوند تا بیشتر به ذخایر پایه روغن روانسازی شوند، یا به عنوان ماده اولیه برای هیدروکراکینگ برای تولید تقطیرهای سبک و میانی. مانند سوخت جت، نفت سفید و گازوئیل. هر روغن باقیمانده در ستون تقطیر خلاء برای پالایش بیشتر به واحد کوکر منتقل می شود.
شیرآلات
دریچه وسیله ای مکانیکی است که با باز کردن، بستن یا مسدود کردن جزئی یک یا چند درگاه یا گذرگاه، جریان یک سیال (مانند مایعات، گازها، جامدات سیال یا دوغاب) را تنظیم، هدایت یا کنترل می کند. شیرها برای ایمنی فرآیند بسیار مهم هستند و به همان توجه به جزئیات نیاز دارند که سایر تجهیزات ثابت یا اجزای سیستم لوله کشی.
هر نوع شیر متفاوت است و نیاز خاصی را در یک مرکز برآورده می کند. دانستن تفاوت بین انواع دریچه و آناتومی فردی آنها برای درک کاربرد مناسب و مشکلات احتمالی مرتبط با هر نوع مهم است.
انواع شیرهای رایج عبارتند از شیرهای دروازه ای، گلوبی، پلاگین، توپی، دیافراگمی، پروانه ای، چک و کشویی. آنها در اندازه های استاندارد لوله، مواد، ضخامت و درجه بندی فشار ساخته می شوند. بدنه دریچه ها معمولاً ریخته گری، آهنگری، ماشینکاری یا جوشکاری می شوند. سطوح نشیمنگاه می توانند یکپارچه باشند یا به صورت درج ساخته شوند. درج ها اجازه می دهند که مواد صندلی با مواد بدنه متفاوت باشد. به عنوان مثال، فلنج بدنه فولاد کربنی ممکن است دارای درج های صندلی از جنس فولاد ضد زنگ باشد تا در طول زمان سایش و پارگی به حداقل برسد. بسته به شرایط فرآیند و مشخصات لوله کشی، شیرها یا فلنجی، رزوه ای، جوشی سوکتی یا جوشی لب به لب هستند.
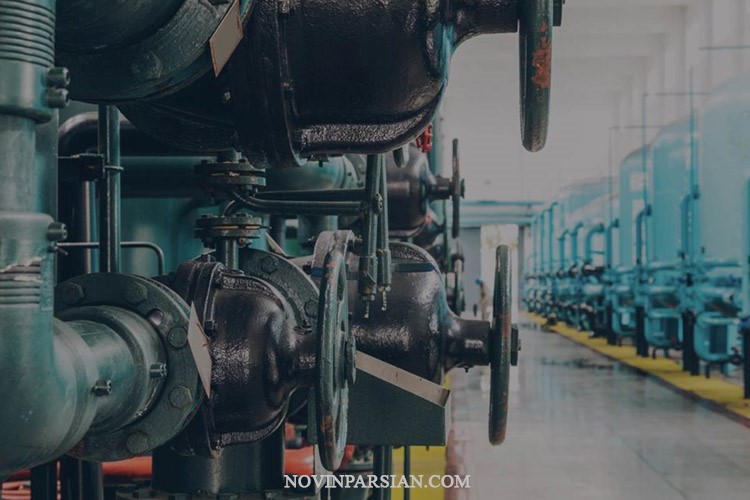
تجهیزات دوار
تجهیزات دوار اصطلاحی است که عموماً در صنایع نفت و گاز برای توصیف تجهیزات و ماشینهایی که از انرژی جنبشی برای جابجایی سیالات، گازها و سایر مواد استفاده میکنند استفاده میشود. قطعات دوره دوار تجهیزات می تواند شامل توربین ها، پمپ ها، ژنراتورها، کمپرسورها ، فن ها، دمنده ها و جعبه دنده ها یا موتورها باشد. این تجهیزات اغلب جدا از سایر تجهیزات ثابت که ممکن است عملکرد مشابهی را انجام دهند، اما طراحی، بهره برداری، نگهداری و الزامات نظارتی متفاوتی دارند، کار می کنند.
ژنراتور
ژنراتور الکتریکی که دینام نیز نامیده می شود، هر ماشینی است که انرژی مکانیکی را برای انتقال و توزیع از طریق خطوط برق به مشتریان خانگی، تجاری و صنعتی به برق تبدیل می کند. ژنراتورها همچنین نیروی الکتریکی مورد نیاز برای خودروها، هواپیماها، کشتی ها و قطارها را تولید می کنند.
توان مکانیکی یک ژنراتور الکتریکی معمولاً از یک شفت در حال چرخش به دست میآید و برابر است با گشتاور شفت ضرب در سرعت چرخشی یا زاویهای. نیروی مکانیکی ممکن است از منابع مختلفی حاصل شود: توربین های هیدرولیک در سدها یا آبشارها. توربین های بادی؛ توربین های بخار با استفاده از بخار تولید شده با گرمای حاصل از احتراق سوخت های فسیلی یا از شکافت هسته ای. توربین های گازی که گاز را مستقیماً در توربین می سوزانند. یا موتورهای بنزینی و دیزلی. ساختار و سرعت ژنراتور ممکن است بسته به ویژگی های محرک مکانیکی اولیه متفاوت باشد.
تقریباً تمام ژنراتورهایی که برای تامین شبکه های برق استفاده می شوند جریان متناوب تولید می کنند که قطبیت را در یک فرکانس ثابت معکوس می کند (معمولاً 50 یا 60 سیکل یا معکوس دو برابر در هر ثانیه). از آنجایی که تعدادی از ژنراتورها به یک شبکه برق متصل هستند، برای تولید همزمان باید در فرکانس یکسانی کار کنند. بنابراین آنها به عنوان ژنراتور سنکرون یا در برخی زمینه ها آلترناتور شناخته می شوند.
فن و دمنده
فن ها و دمنده ها در طیف وسیعی از اندازه ها هستند و می توانند جریان گریز از مرکز، محوری و ترکیبی باشند. ساخته شده از آلیاژهای ارتجاعی خاص، قادر به کار در دماهای بالا هستند. از آنها برای جابجایی گازها در ترکیب با سایر قطعات مکانیکی استفاده می شود. همانند سایر تجهیزات دوار، بهره وری عنصر جدایی ناپذیر عملیات است. بین دمنده و فن تفاوت وجود دارد. فن ها جریانی با فشار کمتر و حجم بیشتر تولید می کنند در حالی که دمنده ها نسبت فشار بالا به جریان حجم زیاد تولید می کنند.
دمنده ها تجهیزات نصبی هستند که انتقال هوا را در محیط ساطع شده با فشار زیاد یا کم فراهم می کنند و فن را با نیروی دریافتی از موتور می دوارند.
دمنده یک تجهیزات لوله کشی است که فن را با نیرویی که از موتور دریافت می کند به چرخش در می آورد و هوا را در محیط ساطع شده با دبی زیاد یا فشار کم منتقل می کند. فن در دمنده ها می چرخد و هوا را در قسمت مکش جارو می کند. سپس هوای محبوس شده به سمت خروجی رانده می شود. دمنده ها اغلب برای حرکت هوا استفاده می شوند.
دمنده وسیله ای است که گازها را با انتقال انرژی به بیرون رانده می کند تا فشار و سرعت آن افزایش یابد.
آنها از دمنده های بزرگی که در کاربردهایی مانند ماشین آلات تولید و اتاق های تمیز یافت می شوند تا دمنده های کوچکی که در دستگاه هایی مانند لوازم خانگی یا رایانه های شخصی تعبیه شده اند و برای دمیدن هوا برای تهویه یا خنک کننده استفاده می شوند، متفاوت هستند.
امروزه دمنده ها و کمپرسورها در صنایع مختلف مورد استفاده قرار می گیرند و در تجهیزاتی مانند ماشین آلات سورت یا حمل و نقل و تجهیزات پردازش یا مونتاژ و بسته بندی تعبیه می شوند. آنها همچنین در محصولاتی مانند رایانه و لوازم خانگی یافت می شوند، جایی که کاهش اندازه و افزایش عملکرد را تسهیل می کنند.
کمپرسور
کمپرسورهای گاز تقریباً در تمام جنبه های فرآوری نفت و گاز مورد استفاده قرار می گیرند. نقش مهمی در هزینه های سرمایه ای و عملیاتی دارند. چهار نوع کمپرسور وجود دارد: گریز از مرکز، رفت و برگشتی، جریان محوری و پیچ دوار.
کمپرسورهای سانتریفیوژ عمدتاً در صنایع فرآوری نفت، شیمیایی و گاز طبیعی برای عملکرد بدون وقفه، ایستا و با سرعت بالا استفاده می شوند. اگر به درستی نگهداری شوند می توانند تا ده سال دوام بیاورند. این ماشین ها از یک دیسک دوار برای افزایش سرعت گاز استفاده می کنند. یاتاقان های پشتیبان و مهر و موم های لابیرنت اجزایی هستند که مستعد سایش هستند. آب بندی های تخریب شده می توانند باعث ارتعاشات عملیاتی، دمای بالا و در نهایت خرابی دستگاه شوند.
کمپرسورهای رفت و برگشتی از پیستون به جای پروانه برای توزیع گاز در فشارهای بالا استفاده می کنند. کمپرسورهای رفت و برگشتی چند مرحله ای کارآمدترین کمپرسورهای موجود در بازار در حال حاضر محسوب می شوند. اگر به دنبال کمپرسوری با عمر طولانی، تعمیر و نگهداری کمتر در حین کار و هزینه انرژی کمتر هستید، کمپرسورهای رفت و برگشتی گزینه ی مناسبی خواهند بود.
کمپرسورهای جریان محوری، ماشینهای گازی با فشار مداوم هستند که گاز را با انتشار و شتاب دادن به آن در حالی که ایرفویلها گاز را از گذرگاهها عبور میدهند، فشرده میکنند. آنها راندمان عملیاتی بالا و نرخ جریان انبوه زیادی دارند. آنها در مقایسه با انواع دیگر کمپرسورها به تعداد بیشتری از قطعات نیاز دارند، بنابراین آنها را به یک ماشین پیچیده تبدیل می کند که نیاز به رعایت برنامه نگهداری دقیق دارد.
کمپرسورهای مارپیچ دوار دو پیچ مارپیچ هستند که گاز را با فشار دادن آن به فضای بین مش و سپس فشرده کردن آن با فشار دادن آن از طریق درگاه تخلیه، تحت فشار قرار می دهند. این عمل به طور پیوسته انجام می شود زیرا گاز در امتداد پیچ های دوار مخالف حرکت می کند. هر عبور از فضای بین شبکه و فضای تخلیه گاز را بیشتر تحت فشار قرار می دهد و به یک غبار ریز تبدیل می شود. اینها کمپرسورهای عالی هستند زیرا در مقایسه با کمپرسورهای رفت و برگشتی پیستونی به دلیل حرکت مداوم پیچ ها، نوسان یا ضربان بسیار کمی وجود دارد.
توربین
توربین ها با چگالی توان بالا و قابلیت های عملیاتی با سرعت بالا،نیروی مورد نیاز برای جابجایی مواد را فراهم می کنند. توربین ها معمولاً بخشی از یک ماشین بزرگتر هستند و در ارتباط با سایر اجزای مکانیکی مانند کمپرسورها و فن ها استفاده می شوند. این تجهیزات در حین کار در معرض سایش و کرنش جدی قرار می گیرند و این می تواند منجر به مسائلی مانند تحریک تیغه ها، آسیب ضربه، سایش تیغه ها و شل شدن پره ها شود. صدمات قابل توجهی از شیم های بیرون زده ایجاد می شود که باعث آسیب ضربه به تیغه های پایین دست می شود.
جعبه دنده یا گیر بکس
جعبه دنده اساساً به تغییر یا تغییر سرعت تجهیزات مکانیکی کمک می کند. آنها می توانند سرعت، جهت و گشتاور منبع تغذیه را تغییر دهند. انواع مختلفی از جعبه دنده وجود دارد: حلزونی، مارپیچ، سیاره ای و خار.
چرخ دنده های حلزونی در کاهنده های سرعت استفاده می شود، زیرا آنها قادر به کاهش سرعت زیاد هستند. جعبه دنده های سیاره ای گشتاور بالایی را در طول برنامه های کاهش سرعت ارائه می دهند. گیربکس های حلزونی در هنگام افزایش و کاهش سرعت صدای کمتری دارند و نسبت به گیربکس های حلزونی دوام بیشتری دارند. گیربکس ها در معرض مشکلات نشتی روان کننده، ناهماهنگی، نقص بلبرینگ، عدم تعادل و لرزش قرار دارند.
گیربکس عملکرد کاهش سرعت را دارد. در مقایسه با چرخ دنده های معمولی، دارای مزایای نسبت کاهش زیاد و موقعیت نصب فشرده است.
چرخ دنده ها یکی از پرکاربردترین قطعات مکانیکی هستند و در گیربکس های مکانیکی کاربرد فراوانی دارند. از چرخ دنده های کوچک برای ساعت گرفته تا چرخ دنده های بزرگ برای توربین های کشتی، می تواند به طور قابل اعتماد نیرو را انتقال دهد.
با انتخاب ترکیبی از تعداد دندان های مختلف می توان نسبت سرعت دلخواه و صحیحی به دست آورد. با استفاده از افزایش یا کاهش تعداد ترکیب دنده ها، می توان موقعیت رابطه متقابل بین محورهای چرخشی را آزادانه تغییر داد. می توان از آن برای انتقال بین محورهای مختلف مانند محورهای موازی، محورهای متقاطع و محورهای پلکانی استفاده کرد.
گیربکس نوعی وسیله تغییر سرعت است که از طریق مش بندی دنده های بزرگ و کوچک به اثر تغییر سرعت پی می برد و در تغییر سرعت ماشین آلات صنعتی کاربرد فراوانی دارد. دنده بزرگ روی شفت کم سرعت در گیربکس نصب می شود و دنده کوچک روی شفت سرعت بالا نصب می شود. از طریق مش بندی و انتقال بین دنده ها می توان فرآیند شتاب یا کاهش سرعت را تکمیل کرد.
گیربکس نیروی چرخ باد و نیروی واکنش تولید شده توسط انتقال دنده را تحمل می کند و باید استحکام کافی برای مقاومت در برابر نیرو و گشتاور، جلوگیری از تغییر شکل و اطمینان از کیفیت انتقال را داشته باشد. طراحی بدنه جعبه دنده باید با الزامات چیدمان چیدمان انتقال نیرو، شرایط پردازش و مونتاژ و بازرسی و نگهداری آسان انجام شود. با پیشرفت مداوم و سریع صنعت گیربکس، صنایع و شرکت های مختلف بیشتری از گیربکس استفاده کردند و شرکت های بیشتری در صنعت گیربکس توسعه و رشد کردند.
گیربکس یک جزء مکانیکی مهم است که به طور گسترده در توربین های بادی استفاده می شود. وظیفه اصلی آن انتقال نیروی تولید شده توسط چرخ باد تحت تأثیر باد به ژنراتور و به دست آوردن سرعت مربوطه است. معمولا سرعت چرخش روتور باد بسیار کم است که با سرعت دورانی مورد نیاز ژنراتور برای تولید برق فاصله زیادی دارد.
با توجه به اصل طراحی مدولار ساختار واحد، گیربکس تا حد زیادی انواع قطعات را کاهش می دهد و برای تولید انبوه و انتخاب انعطاف پذیر مناسب است. چرخ دنده مخروطی مارپیچ و چرخ دنده مارپیچ کاهنده همگی از فولاد آلیاژی با کیفیت بالا کربنات و کوئنچ ساخته شده اند
منابع:
https://www.ekinendustriyel.com/blowers/what-is-blower/
https://www.market-prospects.com/articles/what-is-a-gearbox
https://eu.aspina-group.com/en/learning-zone/columns/what-is/007/
https://www.britannica.com/technology/electric-generator
https://petrosadid.com/fixed_equipment/fixed_equipment.php
https://www.pioneerindustrial.com/products/rotating-equipment/