تست مورد نیاز بعد از تعمیرات کمپرسورها
هدف از آزمایش عملکرد تأیید این است که یک کمپرسور مطابق با طراحی سازنده در شرایط عملیاتی ارائه شده در مشخصات عمل می کند. همچنین روشی برای تأیید شکل منحنی جریان هد کمپرسور، راندمان و محدودیتهای حداکثر و حداقل جریان در سرعتهای مختلف ارائه میکند. اغلب یک آزمایش عملکرد تحت شرایط میدانی با گاز و شرایط عملیاتی مشخص انجام می شود. با این حال، اگر تست عملکرد در کارگاه انجام شود، ممکن است به دلیل نگرانیهای ایمنی یا محدودیتهای تاسیسات آزمایش، تست کمپرسور با گاز مشخص شده امکانپذیر نباشد. چه آزمایش در میدان یا در فروشگاه انجام شود، اثبات طراحی کمپرسور توصیه می شود و اغلب برای نشان دادن تعهدات قراردادی و یکپارچگی مکانیکی ضروری است.
اغلب ترکیب گاز مورد استفاده برای تایید عملکرد کمپرسور با گاز مشخص شده متفاوت است. این اغلب بدون در نظر گرفتن اینکه آزمایش در محیط کار یا کارگاه انجام شود، صادق است. برای آزمایشهای میدانی، جایی که ترکیب گاز و شرایط عملیاتی توسط فرآیند تنظیم میشود، باید تنظیماتی در محاسبات انجام شود تا مشخصات طراحی کمپرسور تأیید شود. به طور معمول، یک آزمایش کارگاهی با مخلوطی از گازها که به دقت انتخاب شده و با هم ترکیب شده اند انجام می شود تا گازی را تشکیل دهد که دارای خواص فیزیکی نزدیک به گاز مشخص شده است. حتی با گاز جایگزین، تفاوت هایی باقی می ماند که بر نتایج آزمایش تأثیر می گذارد.
طراحی اصلی کمپرسور محدودیت هایی را برای عملکرد ترمودینامیکی ایجاد می کند. از مهمترین این محدودیت ها می توان به دبی، توان، دما، فشار و سرعت اشاره کرد. محدودیت های طراحی دیگری نیز وجود دارد که معمولاً شناخته شده نیستند، اما بر عملکرد کمپرسور نیز تأثیر می گذارند. این عوامل عبارتند از نسبت حجم، عدد ماخ و عدد رینولدز. این محدودیت ها در طراحی کمپرسور گنجانده شده اند و تحت تأثیر خواص گاز، شرایط عملیاتی و طراحی مکانیکی قرار دارند. برای بررسی محدودیت های طراحی و عملکرد یک کمپرسور، لازم است دستگاه تست شود. برای ماشینهای جدید، این آزمایشها معمولاً در تأسیسات سازنده انجام میشوند. با این حال، آزمایش گاهی اوقات در این زمینه انجام می شود. همچنین ممکن است مفید باشد که به صورت دوره ای یک کمپرسور را برای روند عملکرد دستگاه آزمایش کنید. آزمایش انجام شده در طول راه اندازی، یک خط پایه عملکرد را ایجاد می کند. آزمایشهای میدانی دورهای اغلب برای بررسی عملکرد کلی و تغییرات سیگنالی که ممکن است آسیب مکانیکی، رسوب داخلی یا سایر شرایط رو به وخامت را پیشبینی کند، انجام میشود.
سرویس و نگهداری کمپرسور
فواصل نگهداری مکرر به ساعت و زمان واقعی عملیات بستگی دارد. این بدان معنی است که کمپرسوری که در مدت 6 یا 12 ماه یا تا تعمیرات مکرر بعدی به ساعات کار خود نمی رسد، همچنان نیاز به سرویس دارد زیرا قطعات فرسوده و فیلترهای مختلف در معرض فرآیند پیری هستند. با توجه ویژه به ایمنی عملیاتی و تضمین عملکرد بدون مشکل، توصیه می شود بسته به نوع کارخانه، فواصل نگهداری مشخص شده را رعایت کنید. حداقل فاصله زمانی 1 بار در سال.
هر چند وقت یک بار باید فیلتر هوای فشرده (فیلتر روغن، فیلتر هوا، فیلتر جداکننده خوب، فیلتر هوای فشرده) را تعویض کنم؟
بسته به عنصر فیلتر و عملکرد، عناصر فیلتر باید هر 6 یا حداقل هر 12 ماه یکبار تعویض شوند.
به منظور اطمینان از عرضه مداوم هوای فشرده با کیفیت بالا و کاهش هزینه های انرژی، عناصر فیلتر باید به طور مرتب تعویض شوند.
تعویض روغن
تعویض روغن معمولاً در ارتباط با تعمیر و نگهداری مکرر انجام می شود. روغن کمپرسور معدنی باید هر 4000 ساعت کارکرد تعویض شود. روغن های کمپرسور مصنوعی معمولاً می توانند دو برابر بیشتر کار کنند. اما بسته به شرایط نصب و مکش، فواصل تعویض روغن ممکن است متفاوت باشد. در صورت شک توصیه می شود که شرایط را در آزمایشگاه با استفاده از آنالیز روغن (چک روغن) آزمایش کنید.
اصولاً باید از روغن کمپرسور مورد تایید کارخانه سازنده استفاده شود. روغن کمپرسور در کمپرسور (برای کمپرسورهای اسکرو روغنکاری شده) بیشترین اهمیت را دارد. روغن باید خنک، فشرده و روان شود. با این حال، همچنین نیاز دارد که ملک پس از آن دوباره قابل تفکیک باشد. بسته به کاربرد سیستم می توان از روغن های معدنی به عنوان روغن های مصنوعی یا غذایی نیز استفاده کرد.
تعویض بلبرینگ
مرحله کمپرسور (کمپرسور اسکرو روغن کاری شده) به دلیل طراحی در معرض سایش یاتاقان است. سازندگان بلبرینگ عملکرد در حال اجرا را حدوداً مشخص می کنند. 35000 ساعت کار برای یاتاقان های آنها. بنابراین توصیه می کنیم پس از رسیدن به ساعت کار، بلبرینگ ها را پیشگیرانه تعویض کنید. هنگام انعقاد قرارداد گارانتی (Assure) مبادله پیشگیرانه تنظیم می شود.
آزمایش مخزن
بازرسی مکرر مخازن تحت فشار توسط فرمان ایمنی و بهداشت صنعتی (BetrSichV) تنظیم می شود. این مشخص می کند که هر 5 سال یک بار یک بازرسی بصری و هر 10 سال یک بار تست فشار انجام دهید.
در صورتی که محصول حجم فشار کمتر از 1000 لیتر (حداکثر فشار مجاز مخزن x حجم مخزن < 1000 لیتر) باشد، می تواند توسط شخص ذیصلاح انجام شود: (مهندس خدمات CompAir). بیش از 1000 لیتر، آزمایش توسط یک متخصص از یک سازمان بازرسی تایید شده (ZÜS) مانند TÜV یا DEKRA انجام می شود.
DGUV 3 یک مقررات پیشگیری از حوادث توسط بیمه حوادث اجتماعی آلمان (DGUV) است. DGUV 3 به طور خاص با سیستم های الکتریکی و تجهیزات مورد استفاده تجاری می پردازد. بازرسی مکرر کمپرسورها بر اساس ارزیابی ریسک برای کمپرسورهای هوا است. به عنوان یک قاعده، بازرسی هر 4 سال یکبار انجام می شود. بازرسی می تواند توسط تکنسین سرویس در ارتباط با تعمیر و نگهداری انجام شود.
طول عمر و ایمنی کمپرسور
طول عمر کمپرسور اساساً بر اساس ساعات کارکرد است و نه لزوماً بر اساس سال ساخت. بنابراین، لزوما امکان کمی کردن عمر مفید وجود ندارد. با توجه به پیشرفت های فنی و برنامه های یارانه ای، بهتر است بررسی شود که آیا می توان با جایگزینی یک سیستم قدیمی ارزش افزوده اقتصادی و زیست محیطی ایجاد کرد یا خیر.
این همچنین می تواند با اصلاح سیستم های موجود، به عنوان مثال، به دست آید. با جایگزینی موتورهای الکتریکی کم مصرف یا مقاوم سازی سیستم های بازیابی حرارت.
در طول فرآیند فشرده سازی / انرژی فشرده سازی آزاد می شود که هوای فشرده و روغن کمپرسور را گرم می کند.
مقدار هوای فشرده ای که می تواند از طریق لوله عبور کند به عوامل مختلفی از جمله قطر لوله، مواد و شرایط بستگی دارد
همیشه باید به خاطر داشته باشید که هوای فشرده می تواند خطرناک باشد و بنابراین باید با احتیاط مناسب استفاده شود. حتی تجهیزات هوای فشرده با کیفیت بالا نیز در صورت استفاده نادرست، جابجایی یا نگهداری نادرست می توانند دارای نقص باشند. از آنجایی که هوای فشرده تحت فشار بالایی قرار دارد، در صورت بروز نقص، خطر رفع فشار ناگهانی وجود دارد.
جوشکاری
در صورتی که مخزن یک کمپرسور هوا نیاز به جوش داشته باشد، عملیات جوشکاری باید توسط یک جوشکار دارای گواهینامه ASME انجام شود، زیرا تمام مخازن تحت فشار عرضه شده توسط Ingersoll Rand دارای گواهینامه هستند. بنابراین، کلیه کارهای جوشکاری روی این ظروف نیز باید توسط جوشکاران دارای گواهینامه ASME دوره آموزش جوشکاری انجام شود.
نکات ایمنی و محیط زیستی
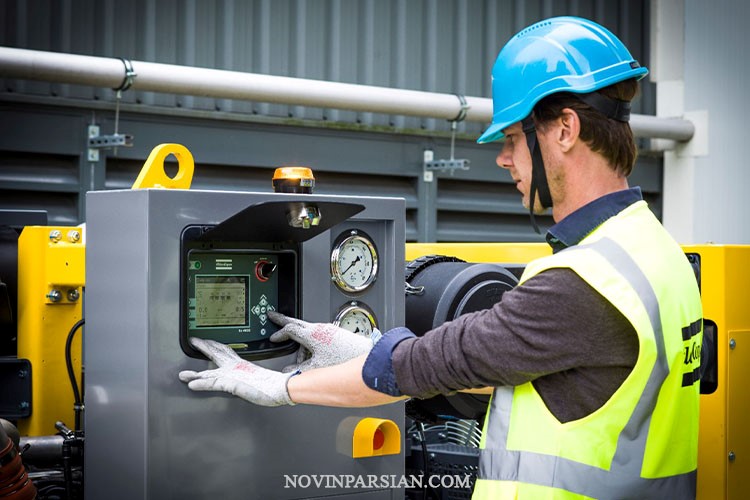
کمپرسورهای هوا هوای محیط را فشرده می کنند. کمپرسورهای هوای برقی هنگام کار، مونوکسید کربن تولید نمی کنند، اما اگر در هوای محیط وجود داشته باشد، مونوکسید کربن را مکیده و آن را فشرده می کنند. اگر در مورد مونوکسید کربن نگرانی دارید، همیشه مقررات مربوطه را بررسی کنید.
اگر مخزن هوا حاوی هوای فشرده باشد، وزن آن بیشتر از زمانی است که خالی باشد. هرگز نباید تجهیزات هوای فشرده را تحت فشار یا متصل به منبع تغذیه حرکت دهید یا روی آن کار کنید.
از نظر زیست محیطی، البته همیشه معقول است که مصرف کنندگان انرژی غیر ضروری را خاموش کنیم. با این حال، با یک خشک کن تبرید، همیشه باید به خاطر داشت که ظرفیت خشک کن بلافاصله پس از روشن شدن خشک کن در دسترس نیست. خشک کن مبرد برای خنک کردن سیستم خود به یک پیش کار نیاز دارد. این زمان در خشک کن های مختلف متفاوت است، بنابراین برای احتیاط باید خشک کن را نیم ساعت قبل از روشن شدن کمپرسور روشن کرد.
اگر نمی توان اطمینان حاصل کرد که خشک کن به موقع راه اندازی شده است، خشک کن باید به طور دائم روشن بماند، زیرا هزینه ها و انرژی مورد نیاز برای حذف میعانات از سیستم لوله کشی بسیار بیشتر از صرفه جویی ممکن با خاموش کردن خشک کن تبرید است.
کد استاندارد تست کمپرسورها
هر کمپرسور مشابه هر تجهیز دیگر دوره تجهیزات دوار چه جدید باشد و چه سالها در خدمت باشد، به احتمال زیاد برای بررسی عملکرد ترمودینامیکی آن آزمایش میشود. برای یک ماشین جدید، آزمایش ممکن است در تاسیسات سازنده تحت شرایط کنترل شده دقیق یا در میدان در شرایط عملیاتی واقعی انجام شود. کمپرسورهای قدیمیتری که پس از تعمیر و نگهداری در خدمت قرار گرفتهاند یا برای مدت طولانی کار کردهاند، ممکن است برای تأیید کارایی و عملکرد عادی نیاز به آزمایش داشته باشند. کد استاندارد ASME PTC-10 نتایج آزمایش دقیق کمپرسور گریز از مرکز را بررسی می کند.
این استاندارد دو قسمتی جنبه های برجسته یک تست عملکرد را بررسی می کند. بخش 1 اهداف تست عملکرد ترمودینامیکی تعیین شده در کد و همچنین سایر عواملی که باید در یک روش آزمایش در نظر گرفته شوند را بررسی می کند. در حالی که این کد در درجه اول برای تست فروشگاه قابل استفاده است، می تواند برای آزمایش میدانی نیز اعمال شود. بخش 2 مفروضات کد و روابط عملکرد اساسی را بررسی می کند. همچنین سه اصل مهم را که بر شرایط عملیاتی تأثیر میگذارند و در نهایت بر صحت تست عملکرد تأثیر میگذارند، بررسی خواهد کرد. این اصول نسبت حجم، عدد ماخ ماشین و عدد رینولدز ماشین هستند.
استاندارد تست عملیاتی ASME PTC-10
روش ارائه شده در کد روشی برای تأیید عملکرد ترمودینامیکی کمپرسورهای گریز از مرکز و محوری ارائه می دهد. این کد دو نوع تست را ارائه می دهد که بر اساس انحراف بین تست و شرایط مشخص شده است. یک روش دقیق برای محاسبه و تصحیح نتایج برای تفاوت در خواص گاز و شرایط آزمایش ارائه شده است. در زیر به طور مختصر اصول راهنمای کد توضیح داده شده است.
آزمایش نوع 1 با گاز مشخص شده در شرایط عملیاتی مشخص شده یا بسیار نزدیک به آن انجام می شود. در حالی که شرایط عملیاتی واقعی و آزمایشی ممکن است متفاوت باشد، انحرافات مجاز محدود هستند.
آزمایش نوع 2 با گاز مشخص شده یا گاز جایگزین انجام می شود. شرایط عملیاتی آزمایش اغلب به طور قابل توجهی با شرایط مشخص شده متفاوت است. شرایط عملیاتی مشمول محدودیت هایی بر اساس طراحی آیرودینامیکی کمپرسور است.
روش محاسبه آزمایش نوع 1 و نوع 2 ممکن است با قوانین گاز ایده آل یا واقعی مطابقت داشته باشد.
این کد همچنین روش هایی را برای محاسبه و تصحیح نتایج آزمون برای تفاوت بین شرایط آزمون و شرایط مشخص ارائه می دهد. همچنین توصیه هایی برای آزمایش دقیق از جمله طرح های تست کمپرسور، ابزار دقیق، پیکربندی لوله کشی و عدم قطعیت ارزش تست ارائه می دهد. در ادامه هر موضوع را خلاصه میکنیم.
محاسبات ترمودینامیکی ممکن است از روش های آنتالپی، ایزنتروپیک یا پلی تروپیک استفاده کنند. این کد معادلات و مثال هایی را برای تعیین کار کمپرسور (که به عنوان هد نیز نامیده می شود)، گاز و بازده کلی، توان گاز و شفت، و تلفات انگلی ارائه می دهد.
این کد یک روش تصحیح برای گازهای آزمایشی و شرایط عملیاتی آزمایشی که از شرایط عملیاتی مشخص شده منحرف شده اند ارائه می دهد.
تست کمپرسور ممکن است حلقه باز یا حلقه بسته باشد. با این حال، نتایج آزمون مشمول محدودیتهایی است که ممکن است به ترتیب آزمون اولویت دهد.
روشهای ابزار دقیق و عدم قطعیتهای اندازهگیری (به استانداردهای سری PTC-19 مراجعه کنید) که برای آزمایش کمپرسورها استفاده میشوند، آورده شدهاند.
توصیه هایی برای طرح لوله کشی نیز گنجانده شده است.
انتخاب گاز آزمایشی
گازهای زیادی وجود دارد که معمولاً برای آزمایش کمپرسورها استفاده می شود. آنها بر اساس خواص فیزیکی، سمیت، اشتعال پذیری و نگرانی های محیطی انتخاب می شوند. سازندگان گاهی اوقات گازهای مختلف را با هم ترکیب می کنند تا با معیارهای هم ارزی و محدودیت های امکانات تست مطابقت داشته باشند.
در زیر توصیه هایی وجود دارد که باید هنگام انتخاب گاز آزمایشی در نظر بگیرید.
- طراحی مکانیکی کمپرسور ممکن است محدودیتهایی را در آزمایش ایجاد کند. هنگام انتخاب گاز آزمایشی، دینامیک روتور ماشین، سرعت بیش از حد، حداکثر دما و محدودیت های توان را در نظر بگیرید.
- از عدم تطابق سرعت جریان پروانه ها جلوگیری کنید. هم ارزی نسبت حجمی مهمترین پارامتر در انتخاب گاز آزمایشی است. این همچنین ممکن است محدودیت هایی در شرایط عملیاتی ایجاد کند.
- وزن مولکولی گاز آزمایش باید دقیقاً با وزن مولکولی گاز مشخص شده مطابقت داشته باشد.
- مقدار k گاز آزمایشی باید دقیقاً با گاز مشخص شده مطابقت داشته باشد تا عدد ماخ ماشین تکرار شود. اگر این عملی نیست، برای جلوگیری از محدودیت های احتمالی استون وال، مقدار k آزمون باید کمی بیشتر باشد.
- یک گاز آزمایشی با حداقل انحراف عدد رینولدز از گاز مشخص شده انتخاب کنید. این کار ضرایب راندمان و اصلاح سر را به حداقل می رساند. این امر به ویژه برای ماشینهایی با عدد رینولدز پایین بسیار مهم است.
API 617 به حداقل پنج نقطه آزمایشی نیاز دارد که باید در سرعت عملیاتی گرفته شود تا نقطه موج، دیوار سنگی، نقطه عملیاتی مورد نیاز و دو نقطه جایگزین را نشان دهد. کاربر ممکن است به صورت اختیاری برای بررسی عملکرد کمپرسور در سرعت های متناوب، نقاط تست اضافی را درخواست کند. به عنوان مثال، نقاط داده اضافی ممکن است برای تأیید خط موج یا شرایط عملیاتی فرآیند بحرانی برای ماشینهای با سرعت متغیر مورد نیاز باشد.
این آزمایش ممکن است به عنوان آزمایش نوع 1 یا نوع 2 انجام شود. نوع 1 معمولاً دقیق تر است و معمولاً زمانی محفوظ می ماند که شرایط آزمایش را بتوان دقیقاً با شرایط عملیاتی مشخص شده مطابقت داد. آزمایش نوع 2 معمولاً یک آزمایش فروشگاهی است که از گاز جایگزین استفاده می کند.
اگر آزمایش نوع 2 توصیه می شود، گاز آزمایش ممکن است یک گاز خالص یا مخلوطی از گازها باشد. ترکیب گاز آزمایش باید قبل از آزمایش توافق شود. علاوه بر این، ترکیب گاز آزمایش باید قبل، حین و بعد از آزمایش نمونه برداری شود. برخی از مخلوطهای گازی تمایل به لایهبندی دارند و نتایج نادرستی میدهند.
خواص فیزیکی گاز آزمایش برای نتیجه بسیار مهم است، به خصوص اگر مخلوطی از گازهای انتخاب شده باشد. توافق بر سر خواص فیزیکی توصیه می شود.
معمولاً در مورد “معادله حالت” که برای محاسبه نتایج آزمون استفاده می شود توافق صورت می گیرد. نه همه برنامههای EOS نتایج یکسانی ارائه میدهند و نه توافقی در صنعت در مورد اینکه کدام روش بهترین است وجود دارد.
درایور خاص مورد استفاده در آزمون را مورد بحث قرار دهید. آیا از درایور مشخص شده استفاده می شود؟ سرعت درایور ثابت خواهد بود یا متغیر؟ اگر سرعت متغیر باشد، موتور، توربین گاز یا توربین بخار خواهد بود؟
اگر یک چرخ دنده بخشی از آزمایش باشد، آیا تولید کننده یا کاربر عرضه می شود؟ آیا کارایی دنده مشخص است؟ برای بررسی کارایی چرخ دنده می توان آزمایشاتی را انجام داد.
آیا گاز با مبدل آب خنک خنک می شود یا هوا خنک؟ آیا محدودیت دمایی در مایع خنک کننده مورد استفاده در آزمایش وجود دارد؟
آیا فشار کاری مجاز تجهیزات ثابت و سیستم های لوله کشی برای آزمایش کافی است؟ آیا برای محافظت از سیستم به شیر اطمینان فشار نیاز است و آیا اندازه آن مناسب است؟
توافق در مورد نحوه اندازه گیری توان ورودی مهم است. گزینه ها عبارتند از تعادل حرارتی، درایور کالیبره شده، دینامومتر و گشتاورسنج. روش خاص اندازه گیری توان ورودی را با سازنده بررسی کنید.
یک شماتیک لوله کشی و ابزار توصیه می شود. نقشه باید جزئیات حلقه آزمایش از جمله محل قرارگیری تجهیزات اصلی، تعداد و مکان ابزارها و اندازه لوله کشی را نشان دهد. این امر به ویژه برای کمپرسورهایی با چند بخش، جریان جانبی ورودی یا پیکربندی پشت سر هم مهم است.
قبل از ادامه آزمون عملکرد، یک روش کتبی توصیه می شود که نحوه انجام آزمون را تشریح می کند. این روش باید به وضوح دامنه آزمایش، مسئولیت های هر یک از طرفین، لوله کشی آزمایشی و چیدمان ابزار، روش های اندازه گیری، محدودیت های عدم قطعیت، کالیبراسیون، گرفتن داده های آزمایش و نحوه تفسیر نتایج و معیارهای پذیرش را به وضوح بیان کند.
همانطور که گفته شد این کد تشخیص می دهد که شرایط آزمایش واقعی و شرایط طراحی مشخص شده ممکن است یکسان نباشند. مفروضات اساسی به گونه ای ساخته شده اند که بتوان نتایج آزمون را با طرح اصلی یا برخی از داده های پایه دیگر مقایسه کرد. به عنوان مثال، یک کمپرسور بسته به جایی که در منحنی جریان سر کار می کند، می تواند کارایی متفاوتی داشته باشد. با این حال، اگر ترکیب گاز و شرایط عملیاتی مشابه طرح اصلی نباشد، نتایج چقدر دقیق هستند؟ این سوال در زیر مورد بحث قرار خواهد گرفت.
پارامترهای مهم دیگری نیز وجود دارد که توسط کد برای تجزیه و تحلیل عملکرد کمپرسور استفاده می شود. دو مورد اول ضریب جریان و ضریب کار نامیده می شوند. اینها پارامترهای بدون بعد هستند که در تفسیر نتایج آزمایش مفید هستند، به ویژه هنگام مقایسه نتایج آزمایش با طرح اصلی یا برخی از داده های دیگر. سه پارامتر مهم دیگر نسبت حجم، عدد ماخ ماشین و عدد رینولدز ماشین نام دارند. این پارامترها تضمین می کنند که خواص آیرودینامیکی یک کمپرسور هر زمان که از گازهای آزمایشی یا شرایط عملیاتی متناوب استفاده می شود، حفظ می شود. علاوه بر این، آنها محدودیت هایی را در محدوده عملیاتی ایجاد می کنند و به اصلاح سر و کارایی برای تلفات اصطکاک کمک می کنند. هر پارامتر به طور خلاصه مورد بحث قرار خواهد گرفت.
پارامترهای بدون بعد
به احتمال زیاد شرایط آزمایش واقعی و شرایط طراحی مشخص شده یکسان نیستند. برای جبران تفاوت ها، کد از پارامترهای بدون بعد به نام ضریب جریان، ضریب کار و ضریب کار کل استفاده می کند. این آئین نامه همچنین در مورد هر ضریب و معادل بودن آنها در آزمون و شرایط مشخص مفروضاتی را ایجاد می کند.
تغییرات در عملکرد کمپرسور را می توان هر زمان که سرعت نوسان داشت، با استفاده از قوانین میل ترکیبی تعیین کرد. اگر جریان کمپرسور، هد و ویژگیهای بازده در یک سرعت معین مشخص باشد، آنگاه صرفاً اعمال قوانین میل ترکیبی در یک سرعت متناوب، منحنی جدیدی تولید میکند که عملکرد کمپرسور را در آن سرعت نشان میدهد. این همان مفهوم پشت سر و ضریب جریان است. در اصل، ضریب جریان نشاندهنده «میزان جریان عادی» کمپرسور در هر سرعتی است. به طور مشابه، ضریب کار و ضریب کار کل نشان دهنده “هد نرمال شده” کمپرسور در هر سرعتی است. قوانین قرابت همچنین دلالت بر این دارد که کارایی ارائه شده در دو شرایط معادل یکسان باقی خواهد ماند. این ویژگی ها نقش عمده ای در تست های فروشگاهی و میدانی کمپرسورهای سانتریفیوژ دارند.
کد سه روش برای تعیین کار کمپرسور (همچنین هد نامیده می شود) را تشخیص می دهد. روش اول روش آنتالپی است. این روش تفاوت در آنتالپی ورودی و تخلیه را نشان می دهد و منجر به کار واقعی ارائه شده به گاز می شود. روش بعدی تعیین کار به روش ایزنتروپیک است. این روش تنها کار ایده آل کمپرسور را تعیین می کند. آخرین رابطه برای تعیین کار کمپرسور، روش پلی تروپیک است. فقط کار ایده آل با این روش پیدا می شود. هر سه روش معمولاً توسط کاربران و سازندگان کمپرسور استفاده می شود.
نسبت حجم
نسبت حجم یک پارامتر مهم آیرودینامیکی است. با تغییر خواص گاز و شرایط عملیاتی، شرایط جریان مشابهی را حفظ می کند. بهترین راه برای توصیف نسبت حجم، در نظر گرفتن یک کمپرسور چند مرحله ای است. جرم گاز ورودی به پروانه اول باید با جرم ورودی به پروانه های دیگر برابر باشد. با این حال، حجم واقعی گاز ورودی به مرحله اول برای سایر پروانه ها یکسان نیست. گاز فشرده و گرم می شود که منجر به کاهش حجم می شود. اگر خواص گاز و شرایط عملکرد گاز آزمایش با گاز مشخص شده متفاوت باشد، حجم ورودی و خروجی از هر مرحله نیز متفاوت خواهد بود. بنابراین، برای تکرار عملکرد آیرودینامیکی یک کمپرسور در شرایط طراحی مشخص شده، شبیه سازی جریان معادل گاز از طریق پروانه ها با تطبیق دقیق نسبت حجم، مهم است.
آزمایش عملکرد کمپرسور گریز از مرکز اغلب با گازی غیر از گاز مشخص شده انجام می شود. علاوه بر این، کمپرسور ممکن است در شرایطی غیر از طراحی اصلی کار کند. برای اطمینان از آزمایش عملکرد دقیق که طراحی اصلی را شبیهسازی میکند، نسبت حجمی گاز مشخص شده باید با نسبت حجمی گاز آزمایش در شرایط عملیاتی مربوطه مطابقت داشته باشد. این آئین نامه محدودیت هایی را برای انحراف از خواص گاز آزمایشی و شرایط عملیاتی تعیین می کند.
هفت متغیر رابطه نسبت حجمی بین گاز آزمایشی و گاز مشخص شده را تعریف می کنند. متغیرها و تأثیری که هر کدام برای افزایش یا کاهش نسبت حجمی دارند. برای مثال، اگر مقدار k گاز آزمایشی بیشتر از گاز مشخص شده باشد، نسبت حجمی کاهش می یابد. به طور مشابه، اگر دمای مکش گاز تست کمتر باشد، نسبت حجم افزایش می یابد. همچنین به یک نکته مهم دیگر نیز توجه کنید و آن این است که تغییرات فشار مکش گاز آزمایش تاثیری بر نسبت حجمی ندارد.
همانطور که قبلا ذکر شد، نسبت حجمی گاز مشخص شده باید با نسبت حجمی گاز آزمایش مطابقت داشته باشد. بنابراین اگر هر یک از خواص فیزیکی گاز آزمایشی بتواند نسبت حجمی را تغییر دهد، چه کاری می توان انجام داد تا دو نسبت حجمی با هم مطابقت داشته باشند؟ یک روش معمول تغییر سرعت تست برای جبران عدم تطابق نسبت حجم است.. توجه داشته باشید که چگونه سرعت کمپرسور کاهش می یابد به طوری که تغییرات نسبت حجم اعمال شده توسط سایر متغیرها به صفر می رسد.
به طور خلاصه، شرایط عملیاتی و خواص فیزیکی یک تست عملکرد باید به دقت بررسی شود. بسیار مهم است که نسبت حجم گاز آزمایشی با نسبت حجمی گاز مشخص شده مطابقت داشته باشد. هر چه نسبت حجم گاز تست به گاز مشخص شده نزدیکتر باشد، نتایج تست عملکرد دقیق تر است.
عدد ماخ
عدد ماخ بر حداکثر مقدار گازی که می تواند برای یک سرعت پروانه معین فشرده شود، تأثیر می گذارد. جریان محدود کننده به عنوان دیواره سنگی شناخته می شود (که به آن جریان چوک نیز می گویند) و معمولاً در منحنی جریان سر جریان مشخصه کمپرسور در شرایط حداکثر جریان برای یک سرعت معین یافت می شود. با افزایش سرعت جریان گاز، سرعت در مسیر جریان داخلی کمپرسور افزایش می یابد تا زمانی که به سرعت صوتی سیال نزدیک شود، بنابراین جریان را محدود می کند. بنابراین، سرعتهای گازی که به عدد ماخ یک نزدیک میشوند، جریان چوک در داخل کمپرسور را نشان میدهند.
این کد اصطلاحی به نام شماره ماخ ماشین را تعریف می کند که نسبت سرعت نوک تیغه خروجی پروانه مرحله اول به سرعت صوتی در شرایط ورودی است. این کد همچنین محدودیت های مجاز را برای انحراف بین اعداد ماخ ماشین گاز مشخص شده و آزمایشی تعیین می کند. این به اطمینان از صحت تست عملکرد کمک می کند. هنگام آزمایش یک کمپرسور، شماره ماخ ماشین در شرایط کار محاسبه شده و با اختلاف گاز مشخص شده و گاز آزمایش مقایسه می شود. برای محدودیت های انحراف مجاز به شکل 2 مراجعه کنید. اگر مقدار از انحراف مجاز بیشتر شود، شرایط عملیاتی گاز آزمایشی ممکن است برای مطابقت با این محدودیت ها نیاز به تنظیم داشته باشد.
عدد رینولدز
اثری که عدد رینولدز بر روی کمپرسور می گذارد مشابه تأثیری است که روی لوله ها می گذارد. گازی که از مسیرهای داخلی یک کمپرسور جریان می یابد، اصطکاک و اتلاف انرژی ایجاد می کند که بر راندمان ماشین تأثیر می گذارد. برای کمپرسورهای گریز از مرکز، کد اصطلاحی به نام شماره ماشین رینولدز تعریف میکند و محدودیتهایی را برای مقادیر مجاز در طول تست عملکرد تعیین میکند. اگر عدد رینولدز ماشین برای شرایط تست و شرایط مشخص شده متفاوت باشد، ضریب تصحیح است. به کارایی آزمون و مقادیر سر اعمال می شود.
منابع: