اصول و مبانی طراحی مبدلهای حرارتی
مبدل های حرارتی وسایلی هستند که با انتقال حرارت بین سیالات در دماهای مختلف انرژی را انتقال می دهند. این دستگاه ها می توانند به طور گسترده هم در زندگی روزمره و هم در کاربردهای صنعتی مانند ژنراتورهای بخار در نیروگاه های حرارتی، تقطیر کننده ها در صنایع شیمیایی، اواپراتورها و کندانسورها در کاربردهای آموزش تهویه مطبوع HVAC و فرآیند تبرید، هیت سینک ها، رادیاتورهای خودرو و احیاگرها در موتورهای توربین گازی مورد استفاده قرار گیرند. در این فصل روش های طراحی اولیه برای دو مبدل حرارتی سیال مورد بحث قرار می گیرد.
مبدل های پوسته لوله ای، کولر هوا و مبدل نوع صفحه ای سه نوع مبدل پرکاربرد در صنایع شیمیایی و فرآیندی هستند. با افزایش تلاش در سال های اخیر برای کاهش وزن و سایز و افزایش کارایی، انواع دیگر مبدل ها به طور فزاینده ای مورد استفاده قرار می گیرند. با این حال، طراحی مکانیکی و حرارتی این مبدلهای جایگزین تمایل به ماهیت اختصاصی دارد که ممکن است توضیح دهد که چرا بسیاری از مشتریان نوع مبدل پوسته و لوله آزمایششده و آزمایششده را ترجیح میدهند که هنوز در اکثر کارخانهها غالب است.
اصول کلی طراحی مکانیکی برای انواع مبدل های زیر ارائه می شود:
- مبدل های پوسته و لوله
- مبدل های هوا خنک
- مبدل های نوع صفحه ای
- مبدل های نوع باله صفحه ای
- مبدل های دو لوله
- مبدل های بلوک گرافیت
- مبدل های نوع صفحه ای مارپیچی
- مبدل های تماس مستقیم
- لوله های حرارتی
انواع کدهای طراحی مبدل های حرارتی
مبدل پوسته و لوله اساساً از تعدادی اجزای متصل تشکیل شده است که برخی از آنها در ساخت انواع دیگر مبدل ها نیز استفاده می شوند. اجزای تحت فشار مبدل پوسته و لوله مطابق با کد طراحی مخازن تحت فشار مانند ASME VIII (1993) یا BS5500 (1994) طراحی شده اند. برای رعایت مقررات مربوطه اجزای تحت فشار انواع مبدل های جایگزین باید حداقل اصول یک کد طراحی مخازن تحت فشار تجهیزات ثابت رعایت شود.
نمی توان انتظار داشت که یک کد طراحی مخزن تحت فشار به تنهایی تمام ویژگی های خاص مبدل های حرارتی را پوشش دهد. برای راهنمایی و حمایت از طراحان، تولیدکنندگان و خریداران، یک کد تکمیلی مطلوب است. یک کد جهانی پذیرفته شده برای مبدل های پوسته و لوله، TEMA (1988) است، که اگرچه برای تکمیل ASME VIII طراحی شده است، اما می تواند در ارتباط با سایر کدهای مخازن تحت فشار استفاده شود. TEMA حداقل ضخامت ها، حد مجاز خوردگی، الزامات طراحی خاص، تلورانس ها، الزامات آزمایش، جنبه های عملیات، نگهداری و ضمانت ها را مشخص می کند. (به استانداردهای TEMA نیز مراجعه کنید.)
یکی از مفیدترین عملکردهای TEMA ارائه یک سیستم سه حرفی ساده است که به طور کامل همه مبدل های پوسته و لوله را با توجه به نوع مبدل، سر انتهای ثابت، سر انتهای عقب و پیکربندی نازل جانبی پوسته تعریف می کند. حرف اول سر انتهای ثابت، حرف میانی نوع پوسته و حرف آخر نوع انتهای عقب را مشخص می کند.
در تعیین TEMA خریدار یکی از سه کلاس را انتخاب می کند:
- کلاس R برای “نیازهای عمومی شدید نفت و کاربردهای پردازش مرتبط”
- کلاس C برای “الزامات عمومی متوسط کاربردهای تجاری و فرآیندهای عمومی”
- کلاس B برای “خدمات فرآیند شیمیایی”.
طراحی تجهیزات مورد نیاز
تجهیزات انتقال حرارت ممکن است بر اساس نوع یا عملکردی که انجام میدهند، مانند چیلر، کندانسور، جوشکننده خنککننده و غیره تعیین شوند. انتخاب نوع پوسته و لوله عمدتاً بر اساس عواملی مانند نیاز به تدارک حرکت تفاضلی بین پوسته و لوله تعیین میشود. ، فشار طراحی، دمای طراحی و ماهیت رسوب سیالات به جای عملکرد. اطلاعات بیشتر در مورد انتخاب انواع، ویژگی های اصلی و طراحی آنها در ساندرز (1988) آورده شده است.
نوع رایج مبدل های پوسته و لوله، نوع لوله ثابت است. این دارای نام TEMA AEM است. اجزای اصلی مبدل های پوسته و لوله مشخص می شود و یک شماره مرجع داده می شود که به توضیحات اجزای زیر مربوط می شود.
اجزای زیر عملکردی را عمدتاً مربوط به جریان سیال انجام می دهند:
لوله ها: محدوده قطر خارجی معمول برای کاربردهای نفتی و پتروشیمی 15 تا 32 میلی متر است که 19 و 25 رایج ترین آنها هستند. لوله ها را می توان با حداقل یا متوسط ضخامت دیوار خریداری کرد. تلورانس ضخامت برای لوله های دیواری حداقل منهای صفر، به اضافه 18 تا 22 درصد ضخامت اسمی است، در حالی که ضخامت لوله های دیواری متوسط، مثبت و منفی 8 تا 10 درصد ضخامت دیواره اسمی است. ضخامت لوله باید در برابر فشار داخلی و خارجی بررسی شود، اما ابعاد لوله های متداول می تواند فشارهای قابل توجهی را تحمل کند. متداول ترین محدوده طول لوله 3600 تا 9000 میلی متر برای بسته های متحرک و 3600 تا 15000 میلی متر برای نوع لوله ثابت است. وزن بسته های قابل جابجایی اغلب به 20 تن محدود می شود. TEMA حداقل نسبت گام لوله به قطر خارجی و حداقل فاصله بین لوله ها را مشخص می کند.
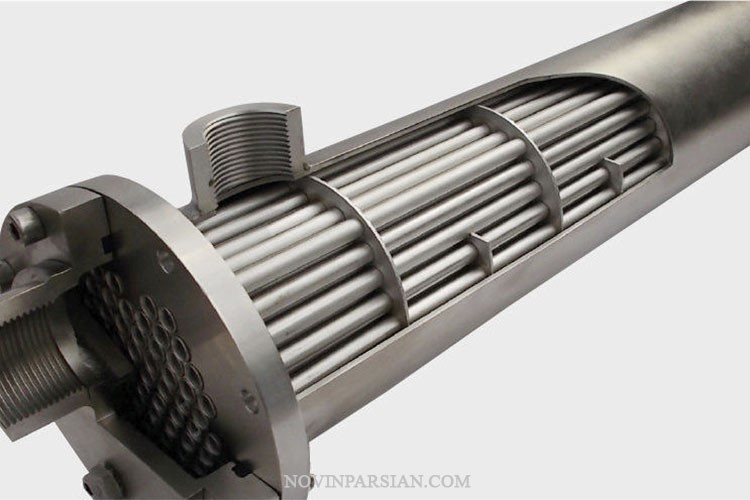
صفحات پارتیشن کانالی: برای مبدلهایی با چندین گذر لوله، کانالها با صفحات فلزی تخت تعبیه شدهاند که سر را به محفظههای جداگانه تقسیم میکنند. ضخامت این صفحات به قطر کانال بستگی دارد اما معمولاً برای فولادهای کربنی و کم آلیاژ 9 تا 16 میلی متر و برای آلیاژهای گران تر 6 تا 13 میلی متر است. به جز هدهای مخصوص فشار قوی، صفحات جداکننده همیشه به لوله کانال و همچنین به لوله یا روکش مجاور جوش داده می شوند، اگر هر یک از این اجزا به نوبه خود به کانال جوش داده شوند. اگر ورق لوله یا پوشش به کانال جوش داده نشده باشد، ورق لوله یا پوشش شیاردار شده و لبه صفحه جداکننده توسط واشر تعبیه شده در شیارها آب بندی می شود.
بافل های صدفی: بافل های متقاطع پوسته هدف دوگانه پشتیبانی از لوله ها در فواصل زمانی برای جلوگیری از افتادگی و ارتعاش و همچنین فشار دادن سیال سمت پوسته به جلو و عقب در سراسر بسته نرم افزاری، از یک سر مبدل به سر دیگر هستند. بافل های تک برش قطعه ای رایج ترین هستند، با این حال، افت حرارتی یا فشار ممکن است باعث ایجاد بافل هایی با شکل پیچیده تر شود. حلقه پشتی را شکافته و از میان مبدلهای سر شناور بکشید دارای یک بافل از نوع پشتیبانی ویژه در مجاورت سر شناور است تا وزن مجموعه سر شناور را تحمل کند. TEMA حداقل ضخامت بافل، حداکثر طول لوله بدون پشتیبانی، فاصله بین لولهها و سوراخهای بافل و بین قطر داخلی پوسته و قطر بیرونی بافل را مشخص میکند. دو مبدل پوسته پاس (شکل 2 نوع پوسته F، G یا H را ببینید) به یک بافل طولی نیاز دارند که برای مبدل های نوع F به صفحه لوله ثابت جوش داده می شود. نشت سیال سمت پوسته بین پوسته و لبه های بافل طولی باید به حداقل برسد. هنگامی که از بسته های قابل جابجایی استفاده می شود، این شکاف نشتی توسط نوارهای انعطاف پذیر یا دستگاه های بسته بندی مهر و موم می شود. شکل 3 یک نوار انعطاف پذیر معمولی را نشان می دهد.
میله های کراوات: میله های اتصال و اسپیسرها برای نگه داشتن دسته لوله در کنار هم و برای قرار دادن بافل های پوسته در موقعیت صحیح استفاده می شوند. میله های اتصال میله های فلزی دایره ای هستند که به صفحه لوله ثابت پیچ می شوند و در دورترین بافل توسط مهره های قفلی محکم می شوند. تعداد میله های اتصال به قطر پوسته بستگی دارد و توسط TEMA مشخص می شود.
اجزای زیر عملکردی را انجام می دهند که عمدتاً مربوط به فشار و مهار سیال است. طراحی آنها مطابق با کد مخزن تحت فشار تجهیزات ثابت مربوطه انجام می شود
بشکه پوسته و بشکه کانال: TEMA حداقل ضخامت بشکه را بسته به قطر، جنس و کلاس مشخص می کند. بیشتر بشکه های بزرگتر از 450 میلی متر قطر داخلی از صفحات نورد شده و جوش داده شده ساخته می شوند. بشکه پوسته باید مستقیم و درست باشد زیرا یک بسته لوله محکم باید وارد شود و در ساخت باید دقت خاصی به خرج داد. نازل های بزرگ ممکن است به دلیل انقباض جوش باعث “فروختگی” در محل اتصال نازل پوسته شوند و ممکن است به سفت کننده های موقتی نیاز باشد.
سر مخزن. سرهای مخازنی با قطر کم و فشار کم گاهی ریخته گری می شوند اما بیشتر سرهای بشقابی از صفحه ساخته می شوند و به شکل نیمه بیضی، توری یا نیمکره هستند. حداقل ضخامت سر مخازن مانند بشکه های مجاور است. تمیز کردن لوله با درپوش کانال جوش داده شده (انتهای جلوی TEMA B) نیاز به شکستن و بازسازی فلنج های نازل کانال دارد تا بتوان کانال را جدا کرد. یک سر صاف (انتهای جلوی TEMA A) از این امر جلوگیری می کند و به لوله اجازه می دهد در جای خود باقی بماند.
نازل: اکثر نازل ها به گونه ای اندازه می شوند که با لوله های زمانبندی مجاور مطابقت داشته باشند. منافذ در بشکه ها نیاز به تقویت مطابق با کد مخزن تحت فشار مربوطه دارند که به نوبه خود حداکثر اندازه باز شدن نازل را محدود می کند. یک نازل معمولی در سرویس متوسط توسط یک صفحه تقویت کننده و با فلنج نازل گردن آموزش جوشکاری ارائه می شود.
فلنج: سه نوع فلنج در مبدل های پوسته و لوله یافت می شود، یعنی فلنج های گیره برای بشکه های پوسته و کانال. فلنج های داخلی در مبدل سر شناور برای جداسازی قطعات داخلی و حذف بسته نرم افزاری لوله. و فلنج های نازل که در آن استانداردهای فلنج و واشر، اندازه و درجه فشار توسط مشخصات خط تعیین می شود. شکل 5 سه نوع فلنج را نشان می دهد. نوع فلنج گردن جوش، که دارای یک توپی مخروطی با انتقال تنش صاف و قابل دسترسی برای بررسی کامل غیر مخرب است، بالاترین یکپارچگی را در بین سه نوع ارائه می دهد. فلنج از سه جزء فرعی تشکیل شده است: حلقه فلنج، واشر و پیچ. عملکرد موفقیت آمیز فلنج به انتخاب، طراحی و مونتاژ صحیح این اجزای فرعی بستگی دارد. کتاب طراحی تبادل حرارتی شامل دو فصل است که در مورد این عوامل بحث می کند
Tubesheets: ورق های لوله ای با ضخامت کمتر از 100 میلی متر معمولاً از مواد صفحه ساخته می شوند. صفحات لوله ضخیم تر، یا برای خدمات با یکپارچگی بالا، از دیسک های جعلی ساخته می شوند. ورق روکش معمولاً در مواردی استفاده می شود که مواد آلیاژ بالا به دلایل فرآیند مورد نیاز است. یک ورق لوله دار شامل یک صفحه پشتی کربن یا کم آلیاژ با ضخامت کافی برای برآورده کردن کد طراحی مخزن تحت فشار است که لایه ای از مواد آلیاژی بالاتر با جوشکاری یا روکش انفجاری روی آن چسبانده شده است. TEMA قوانین طراحی را برای محاسبه ضخامت صفحه لوله ارائه می دهد که نتایج مشابه اما نه یکسانی را با قوانین در ASME و BS5500 می دهد. همچنین تلورانس ها را برای قطر سوراخ لوله، عرض رباط و رانش مته مشخص می کند. روش های مختلفی برای اتصال انتهای لوله به صفحه لوله در دسترس است. متداول ترین روش انبساط غلتکی است که در آن نیروی تولید شده توسط یک ابزار منبسط کننده، لوله را به صورت شعاعی به سمت خارج تغییر شکل می دهد تا یک آب بندی مکانیکی ایجاد کند. در انبساط انفجاری یک بار در داخل لوله در ضخامت صفحه لوله قرار می گیرد. گرانتر از انبساط غلتکی است اما می تواند اتصالات محکم تری ایجاد کند. اتصالات لوله جوش داده شده را می توان در وجه “خارجی” ورق لوله یا سوراخ در سطح “داخلی” ورق لوله ایجاد کرد. موفقیت اتصالات انتهای لوله به شدت به انتخاب صحیح نوع و تجربه سازنده بستگی دارد. این موضوع در ساندرز (1988) به تفصیل مورد بحث قرار گرفته است.
دم انبساط: اینها ممکن است در پوسته یک مبدل لوله ثابت یا در سر شناور مبدل های سر شناور تک لوله ای مورد نیاز باشند. آنها با جزئیات بیشتر در اتصالات انبساط مورد بحث قرار می گیرند.
سایر اجزای مهم مبدل حرارتی عبارتند از اجزای موجود در مجموعه های سر شناور، تکیه گاه ها و سربرگ های مستطیلی در کولر های هوایی.
روش های طراحی مبدل های حرارتی
مبدل های حرارتی (HE) وسایلی هستند که انرژی را بین سیالات در دماهای مختلف با انتقال حرارت انتقال می دهند. مبدل های حرارتی ممکن است بر اساس معیارهای مختلفی طبقه بندی شوند. طبقهبندی مبدلهای حرارتی (HE) را در بازیابیکنندهها و احیاکنندهها با توجه به ساخت و ساز استفاده میکند. در ریکپراتورها، گرما به طور مستقیم (فورا) بین دو سیال منتقل می شود و با مخالفت، در احیاکننده ها تبادل حرارتی فوری بین سیال ها وجود ندارد. بلکه از طریق یک مرحله میانی شامل ذخیره انرژی حرارتی انجام می شود. ریکپراتورها را می توان بر اساس فرآیند انتقال در انواع تماس مستقیم و تماس غیر مستقیم طبقه بندی کرد. در تماس غیرمستقیم HE، یک دیواره (جدایی فیزیکی) بین مایعات وجود دارد. ریکاوراتورها به عنوان نوع انتقال مستقیم شناخته می شوند. در مقابل، احیاگرها وسایلی هستند که در آنها تبادل حرارت متناوب بین سیالات گرم و سرد از طریق ذخیره انرژی حرارتی و آزاد شدن از طریق سطح مبدل حرارتی یا ماتریس وجود دارد. احیاگرها اساساً به دو مدل ماتریس دوار و ثابت طبقه بندی می شوند. احیاگرها به عنوان یک نوع انتقال غیر مستقیم شناخته می شوند. در این مطلب روش های طراحی اولیه برای دو مبدل حرارتی سیال مورد بحث قرار می گیرد. ما در مورد روش log-mean تفاوت دما (LMTD)، اثربخشی ε-NTU بحث می کنیم. چهار روش برای تجزیه و تحلیل عملکرد حرارتی بازیابی کننده استفاده می شود: اختلاف دمای میانگین لگاریتم (LMTD)، اثربخشی تعداد واحدهای انتقال (ε-NTU). ، اختلاف دمای میانگین بدون بعد (Ψ-P) و روش های (P1 – P2). در ادامه مراحل روش های طراحی اولیه برای دو مبدل حرارتی سیال مورد بحث قرار گرفته است. تکنیک های طراحی احیاگرها که دو کلاس اصلی هستند مورد بررسی قرار می گیرند. راه حل مشکل بازیابی بر حسب اختلاف دمای میانگین لگاریتم (LMTD) و روش اثربخشی- تعداد واحدهای انتقال (ε-NTU) نیز ارائه شده است.
روش لگاریتم میانگین اختلاف دما (LMTD)
استفاده از این روش به وضوح با آگاهی از دمای ورودی و خروجی سیال سرد و گرم تسهیل می شود. چنین کاربردهایی ممکن است به عنوان مشکلات طراحی مبدل حرارتی طبقه بندی شوند. یعنی مشکلاتی که در آنها دما و نرخ ظرفیت مشخص است و اندازه مبدل مورد نظر است. دو نوع آرایش جریان در یک مبدل حرارتی دو لوله امکان پذیر است: جریان موازی و جریان مخالف. در جریان موازی، هر دو سیال سرد و گرم در یک سر وارد مبدل حرارتی می شوند و در یک جهت حرکت می کنند.
مراحل طراحی با روش LMTD
- نوع مبدل حرارتی را انتخاب کنید.
- هر دمای ورودی یا خروجی ناشناخته و نرخ انتقال حرارت را محاسبه کنید.
- در صورت لزوم، اختلاف دمای میانگین log و ضریب تصحیح را محاسبه کنید.
- ضریب انتقال حرارت کلی را محاسبه کنید.
- مساحت سطح انتقال حرارت را محاسبه کنید.
- طول لوله یا مبدل حرارتی را محاسبه کنید
مراحل طراحی با روش ε – NTU
- نسبت نرخ ظرفیت را محاسبه کنید
- NTU را محاسبه کنید.
- اثربخشی را تعیین کنید.
- نرخ کل انتقال حرارت را محاسبه کنید.
- دمای خروجی را محاسبه کنید.
- برای مشکل سایز بندی ضریب عملکردی را محاسبه کنید.
- نسبت نرخ ظرفیت را محاسبه کنید.
- ضریب انتقال حرارت کلی را محاسبه کنید.
- NTU را تعیین کنید.
- مساحت سطح انتقال حرارت را محاسبه کنید.
- طول لوله یا مبدل حرارتی را محاسبه کنید
اختلاف دمای میانگین بدون بعد (Ψ-P ) و روش (P1 – P2)
مشکل رتبه بندی مبدل یا اندازه را می توان با هر یک از این روش ها حل کرد و در خطای عددی محاسبات راه حل یکسانی را به دست خواهد داد. اگر دمای ورودی، یکی از دمای خروجی سیال و نرخ جریان جرمی مشخص باشد، می توان از روش LMTD برای حل مشکل اندازه استفاده کرد. اگر آنها شناخته نشده باشند، می توان از روش (ε-NTU) استفاده کرد. روش های (Ψ-P) و (P1 – P2) روش های گرافیکی هستند. روش (P1 – P2) شامل تمام پارامترهای اصلی مبدل حرارتی بدون بعد است. از این رو، راهحل مشکل رتبهبندی و اندازهبندی ساده و غیر تکراری است. احیاگرها اساساً به دو مدل ماتریس دوار و ثابت طبقهبندی میشوند و در طراحی حرارتی این مدلها دو روش: 1) تعداد واحدهای انتقال با اثربخشی اصلاح شده (ε-NTUo) و 2) کاهش طول و دوره کاهش یافته (Λ−π) روش هایی برای احیا کننده ها استفاده می شود. (Λ−π) روش عموماً برای احیاگرهای ماتریس ثابت استفاده می شود.
مراحل طراحی با روش Ψ – P
- فاکتور F را محاسبه کنید.
- محاسبه خطوط مقادیر ثابت NTU1 و ضریب F.
- محاسبه میانگین دمای بدون بعد Ψ
- سرعت انتقال حرارت را محاسبه کنید.
منابع