شناخت اجزای تشکیل دهنده کمپرسور های سانتریفیوژ
کمپرسور گریز از مرکز یک ماشین از دوره تجهیزات دوار است که با افزودن انرژی جنبشی به جریان پیوسته سیال از طریق پروانه ها به افزایش فشار دست می یابد. سپس این انرژی جنبشی با کند کردن جریان از طریق یک دیفیوزر به افزایش فشار تبدیل می شود. روتور کمپرسور گریز از مرکز به یک درایور مانند موتور الکتریکی و یا توربین بخار متصل می شود. درایور روتور کمپرسور گریز از مرکز را می چرخاند. پروانه ای که روی روتور متصل است نیز با سرعت بالایی می چرخد. این سرعت بالا و طراحی پروانه آن را قادر می سازد هوا را از مرکز خود به لبه بیرونی پرتاب کند و در مرکز آن خلاء ایجاد کند که به آن “چشم پروانه” نیز گفته می شود. این خلاء هوا را از بیرون از طریق نازل ورودی می کشد. چرخش پروانه فشار گاز را به میزان قابل توجهی افزایش می دهد. سپس هوای با سرعت بالا از لبه بیرونی پروانه چرخان به داخل یک دیفیوزر هدایت می شود. شکل مدام در حال افزایش دیفیوزر باعث کاهش سرعت هوا و در نهایت افزایش بیشتر فشار می شود. افزایش فشار در پروانه تقریبا برابر با افزایش فشار در دیفیوزر است.
اهمیت کمپرسور گریز از مرکز
работни обувки fw34 steelite lusum s1p 38
normamascellani.it
covorase man
bayern münchen spieler
karl sneakers
addobbi fai da te matrimonio
prestonstadler.com
spoločenské šaty pre moletky
fingateau.com
lifeonthevineministries.com
کمپرسور گریز از مرکز اساساً یک دستگاه سیال روتودینامیکی جریان شعاعی است که عمدتاً از هوا به عنوان سیال کار استفاده می کند و با استفاده از آن، کل انرژی داخلی سیال داخل را افزایش می دهد. انرژی مکانیکی معمولاً به صورت افزایش فشار استاتیکی از منبع بیرونی به دستگاه منتقل می شود.
در طول جنگ جهانی دوم، تقریباً تمام واحدهای توربین گازی از کمپرسورهای گریز از مرکز استفاده می کردند. زیرا توجه به ساخت واحدهای توربوجت ساده و سبک معطوف شد زیرا وزن کمتر نیروگاه ها از اهمیت قابل توجهی برخوردار بود. با این حال، پس از جنگ، کمپرسورهای محوری تا حدی ساخته و توسعه یافته اند که
اگرچه امروزه کمپرسورهای گریز از مرکز به اندازه آن روزها محبوب نیستند، علاقه مجددی به مرحله گریز از مرکز که همراه با مراحل تک یا چند محوری استفاده می شود، به ویژه برای موتورهای هواپیماهای توربوفن کوچک و توربوپراپ گسترش یافته است.
ویژگی های کمپرسور گریز از مرکز
فضای بسیار کمتری نسبت به کمپرسور جریان محوری با مشخصات مشابه اشغال می کند.
مقاومت بسیار بهتری در برابر آسیب های ناشی از اجسام خارجی ایجاد می کند.
به دلیل داشتن طول عبور نسبتاً کوتاه، افت عملکرد به دلیل رسوبات تجمعی روی سطوح تیغه کمتر از کمپرسورهای جریان محوری است.
در مقایسه با یک کمپرسور جریان محوری، می تواند به خوبی در محیط های آلوده کار کند.
این توانایی عملکرد در محدوده وسیعی از نرخ جریان جرمی با سرعت چرخشی خاص را دارد.
راندمان آن در مطلوب ترین شرایط برای کارهای مشابه 3 یا 4 درصد کمتر از کمپرسورهای محوری است با این حال، افت بازده کمپرسور جریان محوری نرخ جریان جرمی بسیار پایینی را نشان میدهد.
تیغه ها نسبتا کوچکتر است و بنابراین به نظر می رسد مزیت آن در دست کمپرسور گریز از مرکز به دلیل سادگی و هزینه نسبی آن است.
نحوه عملکرد کمپرسور گریز از مرکز
هنگامی که سیال یا هوا از پروانه چرخان کمپرسور عبور می کند، نیروی یا کار خاصی را تجربه می کند که توسط نیروهای گریز از مرکز انجام می شود. این ورودی کار باعث افزایش فشار و سرعت یا سرعت جریان هوا از طریق پروانه می شود. هوای جاری به محض ورود به بخش پخش کننده سرعت خود را از دست می دهد. با این حال، این دیفیوزر یک جزء ثابت یا ساکن است که در صورت وجود پروانه، هدف جریان هوا را انجام می دهد. با توجه به این کاهش سرعت، افزایش اضافی فشار حاصل می شود. پروانه و دیفیوزر به طور انحصاری حدود 65% و 35% از کل فشار تولید شده توسط کمپرسور را تامین می کنند.
مراحل عملکردی کمپرسور سانتریفیوژ به شرح زیر است:
- پس از راه اندازی، گاز یا هوا از مخزن هوا یا هر منبع دیگری به کمپرسور گریز از مرکز وارد می شود.
- پس از ورود به کمپرسور، هوا به پروانه برخورد می کند که شامل پره های شعاعی متعددی است که با چرخش پروانه می چرخند.
- با برخورد هوا به پره های پروانه، هوا با نیروی گریز از مرکز به مرکز پروانه فشار می آورد.
- پره های پروانه پس از برخورد با هوا انرژی جنبشی به هوا می دهند که باعث افزایش سرعت هوا می شود.
- هوا پس از عبور از پروانه وارد ناحیه دیفیوزر می شود. این دیفیوزر شامل چندین پره ثابت است. به محض ورود هوا به ناحیه پخش کننده، سرعت یا سرعت جریان هوا شروع به کاهش می کند.
- اکنون، طبق اصل برنولی، مربع سرعت با فشار نسبت معکوس دارد. دیفیوزر این افزایش سرعت هوا را قبل از اینکه هوا به مرکز پروانه کشیده شود به انرژی فشار تبدیل می کند. این افزایش فشار پروانه در اکثر شرایط تقریباً برابر با افزایش فشار دیفیوزر خواهد بود.
انواع کمپرسور گریز از مرکز
دو نوع کمپرسور گریز از مرکز وجود دارد.
1. کمپرسور تک مرحله ای
کمپرسورهای تک مرحله ای تنها از یک پروانه تشکیل شده اند که برای جابجایی هوا یا هر گاز دیگر تا نسبت تراکم 3:1 برای فشار یا خلاء استفاده می شود. کمپرسورهای تک مرحلهای دارای طرح تیر یا آرایش پروانهای آویزان هستند که در آن پروانه در انتهای غیر محرک شافت قرار دارد. مزیت اصلی کمپرسورهای تک مرحلهای نسبت به کمپرسورهای چند مرحلهای این است که راندمان بالاتری ارائه میدهند و گاز تحویلی در انتها کاملاً بدون روغن و بدون ولتاژ است.
2. کمپرسور چند مرحله ای
کمپرسورهای چند مرحلهای از دو تا ده پروانه تشکیل شدهاند که میتوانند در انواع پیکربندیهای مسیر جریان با توجه به الزامات خروجی مورد نظر مرتب شوند. دما و نسبت تراکم در هر مرحله ثابت فرض می شود. این کمپرسورها را میتوان در پیکربندیهای مختلفی مانند پیکربندی مستقیم، ترکیبی و جریان دوگانه قرار داد. کمپرسورهای چند مرحله ای نیز در طرح های پرتویی موجود می باشند. با این حال پروانه های آنها بین یاتاقان های شعاعی کمپرسور قرار دارند.
کاربردهای کمپرسور گریز از مرکز
1. صنایع غذایی: از آنجایی که کمپرسورهای سانتریفیوژ می تواند هوای فشرده بدون روغن را فراهم کند، صنایع غذایی بسیار به این نوع کمپرسور بستگی دارد، زیرا هوای فشرده بدون روغن برای برخی از درخواست های حساس ضروری است.
2. توربین های گازی: توربینهای گاز ممکن است از کمپرسور محوری و گریز از مرکز برای به دست آوردن فشردهسازی لازم برای شرایط خاص استفاده کنند.
3. گاز یا هوا فشرده: گاز یا هوای فشرده برای به دست آوردن یا تولید هوای فشرده، کمپرسور گریز از مرکز یکی از ساده ترین و کارآمدترین تجهیزات است و در مواقعی که هوا یا گاز ثابت و بیش از حد مورد نیاز است، بهترین انتخاب است.
4. تبرید و کنترل هوا: از آنجایی که آنها طیف گسترده ای از مبردها و ترمودینامیک را پشتیبانی می کنند و همچنین قادر به تامین تراکم در چرخه های چیلر آب هستند، تقاضاهای زیادی برای استفاده در یخچال ها و تهویه مطبوع دارند.
5. پالایشگاه های نفت، پتروشیمی و کارخانه های شیمیایی: معمولاً برای اهداف فوق از کمپرسور گریز از مرکز با پوشش افقی استفاده می شود و بیشتر آنها کمپرسورهای چند مرحله ای هستند. این نوع کمپرسورها معمولاً توسط موتورهای بخار بزرگ و توربین های گازی کار می کنند.
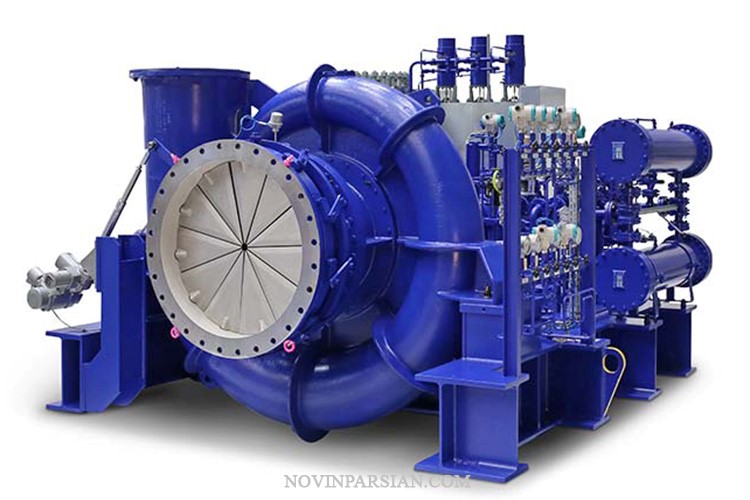
مزایا و معایب کمپرسور های سانتریفیوژ
مزایای کمپرسور گریز از مرکز:
در مقایسه با سایر کمپرسورها تولید آنها آسان است.
کمپرسورهای سانتریفیوژ بسیار کارآمد و قابل اعتماد هستند.
آنها فقط از چند قسمت ساینده تشکیل شده اند و کاملاً بدون روغن هستند.
نسبت فشار بالاتری را در هر مرحله نسبت به کمپرسور جریان محوری ایجاد می کنند.
معایب کمپرسور گریز از مرکز:
فقط می توانند مقدار محدودی فشار ایجاد کنند و برای فشرده سازی بسیار زیاد نمی توان از آن ها استفاده کرد .
به دلیل عملکرد در سرعت های بالاتر، نیاز به نصب ثابت و محکم دارند.
توقف و خفگی از جمله مشکلات رایج آن هاست.
اجزای تشکیل دهنده کمپرسور های سانتریفیوژ
در ادامه به تشریح مهمترین قسمت های کمپرسور های سانتریفیوژ از جمله کاور،پروانه،دیافراگم، بلبرینگ و … خواهیم پرداخت
کیس یا پوشش
تمام اجزای کمپرسور به طور کلی توسط یک محفظه محافظت می شوند. یک کیس متشکل از چندین یاتاقان است که پشتیبانی شعاعی و محوری روتور را فراهم می کند. همچنین شامل چندین نازل به همراه تمامی ورودی ها و اتصالات جریان تخلیه به منظور معرفی و استخراج جریان از کمپرسور می باشد. این کیس محافظ عموما از چدن یا فولاد ساخته می شود
پوشش خارجی ترین قسمت حاوی فشار است. پوشش فلنج های ورودی و خروجی کمپرسور باید برای حداکثر فشار تخلیه کمپرسور درجه بندی شوند. پوشش ها به دو نوع افقی و عمودی تقسیم می شود. روی یک پوشش افقی تقسیم شده، نیمه بالا و پایین در امتداد خط مرکزی پیچ می شوند. تعمیر و نگهداری قسمت داخلی را می توان با برداشتن نیمه بالایی انجام داد. برای این کار، بیشتر اتصالات لولهکشی در نیمه پایینی بدنه تعبیه شده است، به طوری که تعمیر و نگهداری میتواند بدون برداشتن لولههای متصل انجام شود. با این حال، اتصالات فرآیند اصلی ممکن است در نیمه بالایی یا پایینی قرار گیرند.
پوشش عمودی تقسیم شده اغلب دارای یک پوشش بیرونی کامل استوانه ای است. اقلام داخلی مانند مجموعه روتور با چرخاندن آن در داخل آن نصب می شود و سپس سیلندر در امتداد دو طرف با پیچ و مهره بسته می شود.
پوشش های افقی تقسیم شده برای اعمال فشار کم تا فشار تخلیه 40 بار (600 psi) استفاده می شود. پوشش عمودی تقسیم شده تا 800 بار (12000 psi) استفاده می شود. پوشش های کمپرسورهای چند مرحله ای از کربن یا مواد فولادی کم آلیاژ دوره مهندسی مکانیک یا از ریخته گری، آهنگری، صفحه یا ترکیبی از آنها ساخته شده اند.
روتور
روتور یک کمپرسور گریز از مرکز مجموعه ای از شفت، پروانه ها، درام متعادل کننده، یاتاقان رانش، توپی کوپلینگ، آستین ها و حلقه های فاصله ساز است.
شفت
شفت یک بخش سفت است که معمولاً از مواد 40NiCrMo7 دوره ابزار دقیق ساخته می شود. ماشینکاری شده و در قسمت مرکزی پروانه ها و اسپیسرها، دو سر آن بلبرینگ و آب بند نصب شده است.
پروانه
پروانه عنصر چرخان اصلی کمپرسور است که به گاز سرعت می بخشد. شکل و اندازه پروانه بر مشخصات هد و جریان کمپرسور تأثیر می گذارد. پروانه ها روی یک محور فولادی در داخل کمپرسور نصب می شوند و این مجموعه به روتور کمپرسور معروف است. عملکرد روتور این است که از طریق تیغه هایی که به یک دیسک چرخان متصل شده اند، سرعت گاز را فراهم کند. بسته به خروجی مورد نظر، این تیغه ها می توانند متمایل به جلو، شعاعی یا عقب گرد باشند. از آنجایی که تیغه های متمایل به عقب وسیع ترین طیف کارایی را ارائه می دهند، اکثر کمپرسورهای چند مرحله ای از آنها استفاده می کنند.
پروانه سه نوع است:
- پروانه باز: این پروانه ها هیچ پوشش محصوری در قسمت جلو یا عقب ندارند. پروانه های باز برای دبی زیاد در کمپرسور تک مرحله ای استفاده می شود. اینها معمولاً در صنعت فرآیند به غیر از فشرده سازی هوا و گاهی اوقات به عنوان اولین مرحله کمپرسور چند مرحله ای استفاده نمی شوند.
- پروانه نیمه محصور: این نوع از پروانه یک طرف محصور و یک طرف آزاد دارند و صفحه محصور استحکام مکانیکی را اضافه می کند. راندمان بالاتری نسبت به پروانه های باز دارند. پروانه های نیمه محصور همچنین برای دبی زیاد در کمپرسورهای تک مرحله ای و به عنوان مرحله اول در کمپرسورهای چند مرحله ای استفاده می شوند.
- پروانه محصور: در این نوع پره ها در بین 2 دیسک قرار دارند. این پروانه ها عمدتاً در کمپرسورهای چند مرحله ای استفاده می شوند. پروانه بسته و متمایل به عقب که دارای محدوده جریان وسیعی است، رایج ترین پروانه مورد استفاده است.
همچنین با توجه به نحوه وارد کردن گاز توسط پروانه، پروانه ها را می توان به دو دسته تقسیم کرد
- پروانه های تک مکش: گاز را در جهت محوری فقط در یک طرف پروانه می گیرد.
- پروانه های دو مکش: گاز را در جهت محوری در دو طرف پروانه می گیرد. اینها معادل دو پروانه ورودی تکی هستند که پشت به پشت قرار می گیرند و می توانند دو برابر جریان را در همان سر پروانه ورودی تکی تحمل کنند.
دیافراگم
دیافراگم عنصر ثابت داخل محفظه است. این شامل دیفیوزر برای گاز هنگام خروج از پروانه و کانالی برای هدایت مجدد گاز از طریق گذرگاه برگشت به پروانه بعدی است. از طریق ریخته گری ساخته می شود. اینها برای سهولت نصب روتور نصف می شوند. در کمپرسورهای عمودی اسپلیت بشکه ای، نیمه های دیافراگم توسط میله های اتصال در کنار هم قرار می گیرند و بنابراین دو بسته مجزا تشکیل می دهند. پس از نصب روتور آنها به یکدیگر پیچ می شوند. مجموعه حاصل به صورت محوری در محفظه قرار می گیرد. در پوشش افقی تقسیم شده، هر نیمه دیافراگم به تنهایی در دو نیمه پوشش نصب می شود. سطح بیرونی هر دیافراگم دارای یک شیار برای ترکیب با برجستگی مربوطه روی پوشش است. پس از نصب روتور و سایر اجزاء در نیمه پایینی، نیمه بالایی شامل پوشش دیافراگم با یکدیگر پیچ می شوند.
بلبرینگ
در یک کمپرسور روتور توسط یک یاتاقان رانش به صورت محوری در موقعیت خود قرار می گیرد و روی دو یاتاقان ژورنال می چرخد. یاتاقان ژورنال در هر دو انتهای روتور قرار دارد و یاتاقان رانش در خارج از یاتاقان ژورنال و در طرف مقابل کوپلینگ نصب شده است.
یاتاقان رانش
یاتاقانهای رانش برای محدود کردن حرکت محوری استفاده میشوند. یقه رانش به صورت هیدرولیکی به روتور مجهز شده است تا با آن بچرخد. یاتاقانهای رانش دارای یک سطح رانش ثابت، لنتهای رانش و یک یقه رانش هستند که با محور میچرخند. در شرایط عادی یک لایه نازک روغن بین یقه تراست و کفش تراست وجود دارد. هر گونه حرکت محوری توسط کفش های رانش جلوگیری می شود.
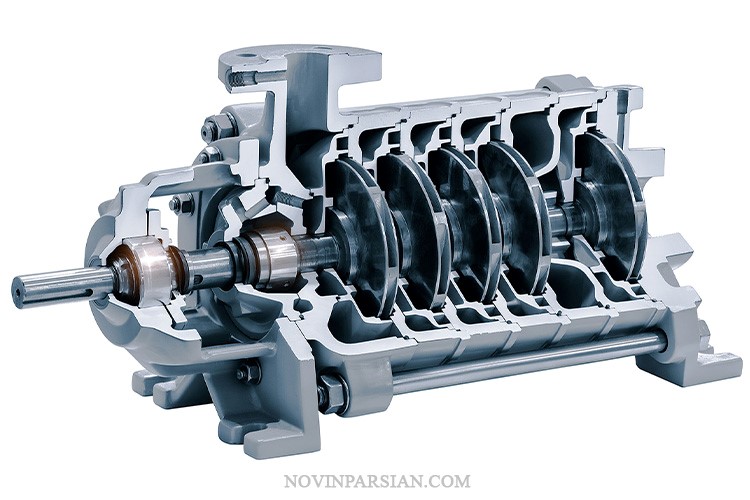
نحوه کار بلبرینگ تراست لنت کج
یاتاقان رانش لنت کج شامل یک حلقه چرخشی است که کفش رانش را نگه می دارد. هر گونه حرکت محوری از یقه شفت در هر دو جهت به دلیل وجود کفشک های تراست جلوگیری می شود. هنگامی که فقط برخی از لنت های رانش بار حرکت محوری را از یقه رانش دریافت می کنند، این بار را به اهرم های تساوی منتقل می کند. سپس تمام اهرمهای تساوی مجدداً طوری تنظیم میشوند که همه لنتها بار مساوی را تحمل کنند. ورودی و خروجی روغن در محفظه یاتاقان وجود دارد. این روغن از تماس یقه رانش و کفشک رانش در شرایط عادی جلوگیری می کند، بنابراین با روانکاری آن از سایش جلوگیری می کند و همچنین به از بین بردن گرمای اضافی و حفظ دمای داخل محفظه یاتاقان در صورت نیاز کمک می کند.
بلبرینگ ژورنال (بیرینگ شعاعی)
یاتاقانهای ژورنال به لایههای مایع روغنی تحت فشار متکی هستند که بین شفت و یاتاقان برای پشتیبانی از شفت چرخان تشکیل میشوند. قسمتی از محور که توسط بلبرینگ پشتیبانی می شود، ژورنال نامیده می شود.
یاتاقان های آستین مستقیم برای واحدهای با سرعت کم با دهانه یاتاقان کوتاه استفاده می شود. نوع دیگری از یاتاقانهای مورد استفاده، یاتاقانهای غلاف سد فشار هستند، اما متداولترین نوع یاتاقانها، بلبرینگهای لنت کجکننده هستند، زیرا برای مقاومت در برابر عملکرد عدم تعادل شرکت روغن مناسب هستند.
نحوه کار بلبرینگ ژورنال پد کج
یاتاقانهای شعاعی پد کجشونده معمولاً از 4 یا 5 پد تشکیل شدهاند که هم به صورت دور و هم به صورت شعاعی توسط پینهای توقف و محوری توسط صفحات انتهایی قرار دارند. پین های توقف نیز به عنوان نازل تامین روغن عمل می کنند. لنت های استاندارد دارای محور مرکزی هستند بنابراین برای هر دو جهت چرخش مناسب هستند. شفت به طور مرکزی در داخل محفظه یاتاقان قرار خواهد گرفت. فاصله کمی بین شفت و لنت های بلبرینگ وجود خواهد داشت. روغن روان کننده تحت فشار به یاتاقان فرستاده می شود و روغن فضای خالی را پر می کند. به دلیل فشار روغن، هر دو لنت و شفت را برای تماس با یکدیگر در حین چرخش شفت محدود می کند. با این حال این به طور ایده آل باعث می شود که شفت در بین دستیابی به یک یاتاقان بدون تماس مورد نظر با سایش و پارگی کمتر شناور شود.
آب بندی شفت
آب بندی در دو انتهای شفت، جایی که شفت از بدنه خارج می شود، استفاده می شود
الف) برای به حداقل رساندن نشت گاز فرآیند (که در حال فشرده شدن است)، از داخل به خارج از کمپرسور.
(ب) برای جلوگیری از ورود هوا یا بخار روغن به کمپرسور و مخلوط شدن با گاز فرآیند.
آب بندی گاز خشک
آب بندی های گاز خشک به دلیل قابلیت اطمینان بالا و کاربرد و مزایای محیطی به استاندارد جدیدی برای کمپرسورهای گریز از مرکز تبدیل شده اند.
نحوه کار آب بندی گاز خشک
آب بندی گاز خشک از دو حلقه جفت تشکیل شده است: یکی از آنها ثابت و دیگری در حال چرخش است. هنگامی که کمپرسور کار نمی کند، از طریق عمل فنر در تماس نزدیک قرار می گیرند. هنگامی که کمپرسور با سرعت بالا میچرخد، نیروهای هیدرودینامیکی ایجاد میکند و حلقه ثابت را به فنر فشار میدهد و یک شکاف کاری حدود 2 تا 5 میکرومتر بین دو حلقه ایجاد میکند. گاز آب بند خارجی که فشار کمی بالاتر از گاز داخل کمپرسور دارد به سیستم آب بندی فرستاده می شود. این گاز آب بندی فضای بین حلقه دوار و هزارخار اول (در مجاورت سمت گاز فرآیند) را تحت فشار قرار داده و آب بندی می کند. قسمت اعظم آن به داخل کمپرسور منتقل می شود اما به دلیل محدودیت ارائه شده توسط لابیرنت، فرآیند ورورد به داخل کمپرسور بسیار کند خواهد بود و همیشه یک فشار مثبت در داخل سیستم آب بندی وجود خواهد داشت. گاز آب بندی تعادل از طریق شکاف کاری حرکت می کند و به عنوان یک سیال کار عمل می کند. از آنجایی که شکاف کاری بسیار نازک است، گاز آب بندی که از آن خارج می شود بسیار کمتر خواهد بود. هر گاز آب بندی که از این طریق خارج شود، به یک سیستم هواکش فرستاده می شود.
این چیدمان همچنین نیازی به روغن کاری ندارد زیرا هر دو حلقه با یکدیگر تماس ندارند. حلقه ثابت در داخل جعبه آب بندی با استفاده از حلقه های O آب بندی می شود. قرار دادن دو یا چند مورد از این آرایش سیل خشک را به صورت سری آب بندی خشک پشت سر هم می نامند.
آب بندی گاز پشت سر هم دارای دو سیستم آب بندی خشک است. اولی سیل اولیه گاز نامیده می شود، هر نشتی از آن به سیستم دریچه تخلیه می شود. دومی آب بندی ثانویه نامیده می شود و اگر آب بندی اولیه از کار بیفتد به عنوان یک پشتیبان عمل می کند.
داخل کاسه نمد گاز خشک یک آب بندی لابیرنت داخلی است که گاز فرآیند را از آب بندی گاز جدا می کند. گاز اولیه خارجی به آب بند اولیه عرضه می شود، همانطور که در مورد آن صحبت شد، بیشتر آنها به کمپرسور می روند و مقدار بسیار کمی از سطح دوار و ثابت عبور می کند و سپس به دریچه اولیه تخلیه می شود. گاز ثانویه به آب بندی ثانویه عرضه می شود. مقداری از آن از لابیرنت میانی عبور می کند و از دریچه اولیه تخلیه می شود. این عمل همچنین مانع از عبور گاز آب بند اولیه به داخل دریچه ثانویه از لابیرنت میانی می شود. مقدار کمی از گاز آب بند ثانویه نیز از طریق شکاف بین عنصر صورت چرخان و ثابت موجود در داخل آب بندی ثانویه عبور می کند و در نهایت از طریق دریچه ثانویه تخلیه می شود. در مجاورت این کارتریج آب بندی در محور کمپرسور محفظه یاتاقان وجود دارد. برای جلوگیری از عبور روغن روانکار از داخل سیستم آب بندی و مخلوط شدن با گاز فرآیندی، گاز جداسازی مانع تامین می شود. فشار گاز جداسازی از ورود روغن از لابیرنت مجاور محفظه یاتاقان جلوگیری می کند و مقداری از آن از لابیرنت داخلی عبور کرده و از دریچه ثانویه خارج می شود.
آب بندی های لابیرنت
آب بندی های لابیرنت دارای برجستگی های لبه های تیز زیادی هستند که روی قطر بیرونی شفت دوار یا قطر داخلی آب بندی شفت ماشین کاری شده اند. آب بندی های لابیرنت ممکن است دوار یا ثابت باشند. آب بندی با افت فشار در هر پشته به دست می آید زیرا مقدار کمی گاز نشت می کند. عمل آب بندی نتیجه مقاومت جریان با کاهش تدریجی آن در سراسر دندانه های لابیرنت است.
درام تعادل:
در یک کمپرسور گریز از مرکز از آنجایی که فشار در سمت تخلیه بیشتر از فشار در سمت مکش است، یک نیروی محوری خالص یا نیروی رانش به سمت مکش اعمال می شود. این نیروی محوری خالص فشار تخلیه Pd- فشار مکش Ps خواهد بود.
برای توضیح واضح، فشار مکش Ps روی پروانه وارد می شود و در آن به P1 در نوک پروانه افزایش می یابد. P1 در سمت مکش پروانه 1 و به طور کامل در سمت تخلیه پروانه 1 و سپس در سمت مکش پروانه دوم عمل می کند. در نوک پروانه دوم به P2 تبدیل می شود و چرخه تا پروانه تخلیه ادامه می یابد.
نیروها یکدیگر را خنثی می کنند و نیروی محوری خالص Pd-Ps روی شفت به سمت مکش وارد می شود. اگر این نیرو بسیار کمتر باشد، یاتاقان رانش می تواند این را محدود کند. اما مانند بسیاری از موارد برای کمپرسور چند مرحله ای، نیروی محوری خالص زیاد خواهد بود.
اکنون برای مقابله با آن یک درام تعادل در سمت تخلیه اضافه می شود. سمت تخلیه درام تعادل از طریق یک قرقره لوله خارجی به سمت مکش متصل می شود تا در سمت تخلیه فشاری برابر با Ps مکش داشته باشد. همچنین در طرف دیگر درام تعادل فشار تخلیه Pd عمل می کند.
با اضافه کردن این آرایش، نیروی محوری خالص دیگری Pd-P خواهیم داشت. از آنجایی که این نیروی خالص در جهت مخالف به سمت تخلیه عمل می کند، Pd-P های مشتق شده قبلی که به سمت مکش عمل می کنند را خنثی می کند. هر نیروی باقیمانده ای که به دلایل دیگر ایجاد شود، اکنون می تواند توسط یاتاقان رانش مراقبت شود.
کوپلینگ
کوپلینگ برق را از درایور به کمپرسور منتقل می کند. کوپلینگ می تواند مستقیم یا از طریق دنده افزایش سرعت باشد. معمولاً کوپلینگهای دندانهدار با تغذیه اجباری یا روانکاری پرکننده استفاده میشوند. کوپلینگ ها با روانکاری تغذیه نیرو برای سرعت چرخش بالا طراحی شده اند و در بیشتر موارد فقط در کمپرسورها استفاده می شوند. نوع دیگری از کوپلینگ ها آب بندی می شوند، معمولاً با گریس روان کننده که هر چند وقت یکبار پر می شود. این کوپلینگ ها فقط در شفت های محرک با سرعت پایین تر استفاده می شوند.
دیفیوزر
پروانه گاز را با سرعت بالا به داخل یک گذرگاه پخش کننده که فضای کوچکی بین دیافراگم های مجاور است که به طور معمول جریان گاز را 180 درجه تغییر می دهد تا آن را به سمت پروانه بعدی هدایت کند، خارج می کند. دیفیوزر معمولا از دو دیوار تشکیل شده است که یک کانال شعاعی ایجاد می کند. به دلیل این آرایش، سرعت گاز کاهش یافته و فشار دینامیکی آن به فشار استاتیکی تبدیل میشود. معابر پخش کننده.
کلکتور
در پروانه مرحله آخر، گاز جمع آوری شده و به فلنج تخلیه تحویل می شود. بخشی که برای جمع آوری گاز تخلیه شده از طریق دیفیوزر به کار می رود، کلکتور نامیده می شود. کلکتور همچنین حاوی دریچههای خاصی و ابزار دقیق دیگری است که هدف کنترل کمپرسور را انجام میدهند.
منابع:
https://thepipingtalk.com/centrifugal-compressor-parts-their-function/