تجهیزات پایپینگ
سیستم لوله کشی و پایپینگ به طور کلی شامل اتصال کامل لوله ها، از جمله اجزای درون خطی مانند اتصالات لوله و فلنج ها در نظر گرفته می شود. پمپ ها، مبادلات حرارتی، شیرها و مخازن نیز بخشی از سیستم لوله کشی محسوب می شوند. سیستم های لوله کشی شریان های فرآیندهای صنعتی ما هستند و سهم سیستم های لوله کشی در یک جامعه صنعتی ضروری است. سیستم های لوله کشی بخش قابل توجهی از کل هزینه کارخانه را به خود اختصاص می دهند که در مواقعی به اندازه یک سوم کل سرمایه گذاری است. سیستمهای لولهکشی که در یک منطقه بسیار محدود چیده شدهاند میتوانند چالشی برای مهندسین لولهکشی و پشتیبانی باشند.
طراحی اولیه یک سیستم لوله کشی با الزامات عملکردی لوله کشی یک سیال از یک نقطه به نقطه دیگر ایجاد می شود. طراحی دقیق بر اساس معیارهایی مانند نوع سیال مورد انتقال، افت فشار مجاز یا اتلاف انرژی، سرعت مورد نظر، محدودیتهای فضا، الزامات فرآیند مانند تخلیه آزاد یا نیاز به اجرای مستقیم، تحلیل تنش، دمای سیال و غیره تعیین میشود. سیستم های لوله کشی نیاز به مهندسی، طراحی، ساخت و نصب قابل توجهی دارد. در برخی موارد، سازههای ویژه مانند T سازهای یا L معکوس، کنسولها، درگاههای U، پایهها و غیره باید صرفاً به منظور پشتیبانی از سیستمهای لولهکشی ساخته شوند.
مواد لوله کشی
مواد مورد استفاده برای ساخت لوله باید متناسب با شرایط عملیاتی سیستم لوله کشی انتخاب شود. راهنمای انتخاب مواد صحیح را می توان از کدهای استاندارد لوله کشی به دست آورد. به عنوان مثال، کد ASME برای لوله کشی تحت فشار شامل بخش هایی در مورد لوله کشی نیرو، لوله کشی صنعتی گاز و هوا، لوله کشی پالایشگاه و نفت و تبرید است.
سیستم های لوله کشی هدف این است که اطمینان حاصل شود که مواد مورد استفاده تحت شرایط عملیاتی فشار، دما، خوردگی و فرسایش مورد انتظار کاملاً ایمن هستند. برخی از موادی که بیشتر برای لوله کشی نیروگاه استفاده می شوند در بخش های زیر مورد بحث قرار می گیرند.
- فولاد: فولاد پرمصرف ترین ماده برای لوله کشی است. فولاد آهنگری به طور گسترده برای اتصالات استفاده می شود در حالی که فولاد ریخته گری عمدتاً برای کاربردهای خاص استفاده می شود. لوله در دو دسته اصلی بدون درز و جوشی تولید می شود.
- چدن : چدن مقاومت بالایی در برابر خوردگی و سایش دارد و برای سیستم های انتقال خاکستر، خطوط فاضلاب و خطوط آب زیرزمینی استفاده می شود. با این حال، بسیار شکننده است و برای اکثر خدمات نیروگاهی مناسب نیست. در گریدهای مختلف از جمله چدن خاکستری، چدن چکش خوار و چدن داکتیل ساخته می شود.
- برنج و مس: مواد غیر آهنی مانند مس و آلیاژهای مس در نیروگاه ها در تجهیزات ابزار دقیق و خدمات آب استفاده می شود که در آن دما عامل اصلی نیست.
اندازه لوله های تجاری
لوله های تجاری در اندازه های استاندارد آموزشگاه فنی ساخته می شوند که هر کدام دارای چندین ضخامت دیواره یا وزن متفاوت هستند. تا و از جمله لوله 304.8 میلی متر (12 اینچ)، اندازه به عنوان قطر داخلی اسمی (تقریبی) بیان می شود. در بالای 304.8 میلی متر، اندازه به عنوان قطر خارجی واقعی داده می شود. تمام کلاس های لوله با اندازه معین دارای قطر خارجی یکسان و ضخامت اضافی هستند
برای وزن های مختلف در داخل به عنوان مثال، اگر یک لوله به اندازه 152.4 میلی متر تعیین شده باشد، به این معنی است که قطر داخلی اسمی یا تقریبی آن 152.4 میلی متر است. قطر خارجی 168.28 میلی متر است. این یک مقدار ثابت است بدون توجه به ضخامت دیوار. قطر داخلی واقعی لوله به ضخامت دیواره آن بستگی دارد. برای یک دیوار استاندارد
ضخامت، قطر داخلی واقعی لوله 152.4 میلی متر 154.06 میلی متر است. برای ضخامت دیواره بسیار قوی، قطر داخلی واقعی 146.34 میلی متر است.
دو سیستم برای تعیین ضخامت دیواره های مختلف در اندازه های مختلف لوله استفاده می شود. روش قدیمیتر لوله را بهعنوان استاندارد (S)، بسیار قوی (XS) و دو برابر قوی (XXS) فهرست میکند. روش جدیدتر، که جایگزین روش قدیمی تر است، از اعداد برنامه برای تعیین ضخامت دیوار استفاده می کند. این اعداد عبارتند از 10، 20، 30، 40، 60، 80، 100، 120، 140 و 160. در اکثر سایزهای لوله، جدول 40 مطابق با استاندارد و جدول 80 مربوط به قدرت فوق العاده است.
لوله و اتصالات
اتصالات در سیستم های لوله برای اتصال بخش های مستقیم لوله، سازگاری با اندازه ها یا اشکال مختلف و برای اهداف دیگر، مانند تنظیم (یا اندازه گیری) جریان سیال استفاده می شود. اتصالات لوله (به ویژه انواع غیر معمول) برای نصب نیاز به پول، زمان، مواد و ابزار دارند و بخش مهمی از سیستم های لوله کشی و لوله کشی هستند. شیرها از نظر فنی اتصالات هستند، اما معمولاً به طور جداگانه مورد بحث قرار می گیرند. اتصالات را می توان به طور کلی به صورت زیر بیان کرد:
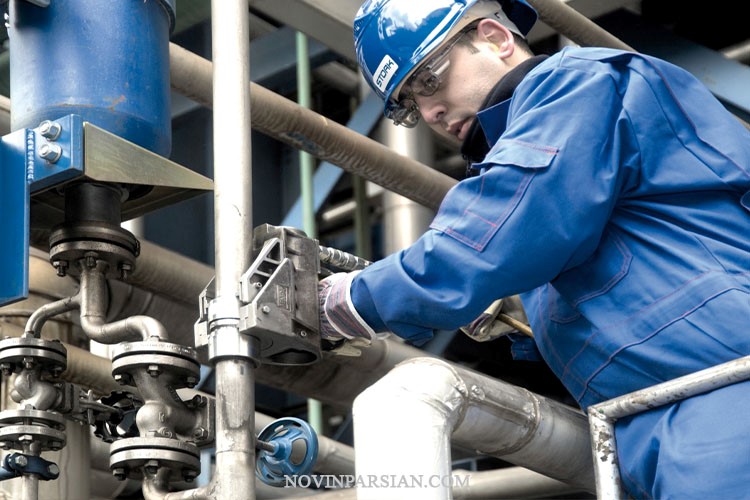
- زانو – برای ایجاد چرخش زاویه ای در لوله کشی.
- نیپل – برای ایجاد اتصالات نزدیک. آنها در هر دو انتها با نخ بسته در تمام طول آن رزوه می شوند.
- کوپلینگ – برای اتصال دو قطعه لوله هم اندازه در یک خط مستقیم.
- یونیون – برای ارائه روشی آسان برای از بین بردن لوله کشی.
- سه راهی و صلیب – برای ایجاد اتصالات خط انشعاب در 90 درجه.
- خم Y – برای ایجاد اتصالات خطوط انشعاب در 45 درجه.
- خم های برگشتی – برای معکوس کردن جهت اجرای لوله.
- درپوش – برای بستن انتهای لوله باز یا اتصالات.
- بوشینگ – برای اتصال لوله های با اندازه های مختلف. انتهای نر در یک کوپلینگ قرار می گیرد و لوله کوچکتر سپس به انتهای مادگی پیچ می شود. اتصال کوچکتر ممکن است به صورت غیر عادی ضربه زده شود تا امکان تخلیه آزاد آب فراهم شود.
- مبدل – برای کاهش اندازه لوله. دارای دو اتصال مادگی است که لوله های با اندازه های مختلف در آن قرار می گیرند. همچنین ممکن است با یک اتصال غیرعادی برای تخلیه رایگان آب ساخته شود.
روش های اتصال لوله
سه روش کلی برای اتصال یا اتصال طول لوله های تحت فشار استفاده می شود. اینها هستند:
- اتصالات پیچی
- اتصالات فلنج دار
- اتصالات جوش داده شده
هر یک از این روش ها دارای مزایا و معایب خاصی هستند که در قسمت های بعدی به بررسی هر کدام می پردازیم.
- اتصالات پیچی: در این روش در هر انتهای لوله رزوه هایی بریده می شود و برای اتصال طول ها از اتصالات پیچی مانند اتصالات، کوپلینگ و زانویی استفاده می شود. این روش عموماً برای اندازه لوله های کمتر از 101.6 میلی متر (4 اینچ) برای فشارهای کم و متوسط استفاده می شود. این مزیت را دارد که لوله کشی را می توان به راحتی جدا یا مونتاژ کرد. با این حال، اتصالات رشته ای در معرض نشتی قرار می گیرد و با بریده شدن رزوه ها در دیواره لوله، استحکام لوله کاهش می یابد.
- اتصالات فلنج دار: در این روش از فلنجهایی در انتهای لوله استفاده میشود که معمولاً با یک واشر بین دو وجه، رو به رو به یکدیگر پیچ میشوند. اتصالات فلنجی مزیتی نسبت به اتصالات جوشی دارند که اجازه جداسازی قطعات را می دهند و راحت تر از اتصالات پیچی جمع آوری و جداسازی می شوند. به منظور جلوگیری از نشتی در اتصالات فلنجی، صفحات فلنج که به هم چسبیده اند، باید کاملاً صاف و صاف باشند. در حالی که از نظر تئوری می توان چهره ها را به این شرایط خرد کرد، اما این یک پیشنهاد وقت گیر و پرهزینه است. بنابراین معمولاً از واشرها بین سطوح فلنج استفاده می شود. واشرها از مواد نسبتاً نرمی ساخته شدهاند که وقتی اتصال فلنجی سفت میشود، فرورفتگیهای کوچک در سطح فلنج را پر میکند و در نتیجه از نشتی جلوگیری میکند.
- اتصالات جوشی: در این روش، طول لوله ها مستقیماً به یکدیگر و مستقیماً به هر شیر یا اتصالاتی که ممکن است مورد نیاز باشد جوش داده می شود. استفاده از این اتصالات جوشی برای لوله کشی مزایای متعددی نسبت به استفاده از اتصالات پیچی یا اتصالات فلنجی دارد:
- با از بین بردن اتصالات پیچی یا فلنجی احتمال نشتی از بین می رود.
- وزن سیستم لوله کشی به دلیل حذف فلنج ها یا اتصالات اتصال کاهش می یابد.
- هزینه مواد و نیاز به نگهداری با حذف فلنج ها و اتصالات کاهش می یابد.
- لولهها مرتبتر به نظر میرسند و با حذف فلنجها و اتصالات حجیم عایقتر میشوند.
- اتصالات جوشی به طراحی لوله کشی انعطاف بیشتری می بخشد زیرا لوله ها ممکن است عملاً در هر زاویه ای به یکدیگر متصل شوند.
- عیب اصلی استفاده از اتصالات جوشی برای لوله کشی، نیاز به دستیابی به جوشکار ماهر در زمان اتصال است.
تکیه گاه
لوله کشی باید به گونه ای حمایت شود که از حمل وزن آن توسط تجهیزات دوره مهندسی مکانیک که به آن متصل است جلوگیری شود. تکیه گاه های مورد استفاده باید از افتادگی بیش از حد لوله جلوگیری کرده و در عین حال اجازه حرکت آزاد لوله را در اثر انبساط یا انقباض بدهد. آرایش نگهدارنده باید طوری طراحی شود که وزن لوله، شیرها، اتصالات و عایق به اضافه وزن سیال موجود در لوله را تحمل کند. انواع مختلف تکیه گاه لوله در ادامه توضیح داده می شوند:
- لوله کشی زهکشی: در مورد لوله کشی بخار، تخلیه دائمی میعانات از خطوط ضروری است. اگر این کار انجام نشود، میعانات گازی همراه با بخار حمل می شود و ممکن است چکش آب ایجاد کند و احتمالا لوله ها یا اتصالات را پاره کند. علاوه بر این، ورود بخار حامل رطوبت به توربین ها یا موتورها بسیار نامطلوب است. دستگاه های مختلفی برای حذف این میعانات و رطوبت از خطوط استفاده می شود که در قسمت های بعدی به بررسی آنها می پردازیم.
- جدا کننده های بخار: جداکنندههای بخار که گاهی اوقات تصفیهکننده بخار نامیده میشوند، دستگاههایی هستند که با نصب در خط بخار، قطرات رطوبت و سایر ناخالصیهای معلق را از بخار خارج میکنند. برای انجام این کار، جداکننده یا باعث می شود که بخار به طور ناگهانی جهت جریان خود را تغییر دهد یا حرکت چرخشی را به بخار منتقل می کند. هر دوی اینها باعث می شود که رطوبت و سایر ذرات از جریان بخار به بیرون پرتاب شوند.
- تله های بخار: هدف از تله بخار تخلیه آب میعان از خطوط بخار، جداکننده ها و سایر تجهیزات بدون اجازه خروج بخار است. علاوه بر این، بیشتر تله ها برای تخلیه هوای موجود در خطوط یا تجهیزات طراحی شده اند. تله های بخار باید در خطوطی نصب شوند که میعانات باید به همان سرعتی که انباشته می شود تخلیه شود، و هر جا که میعانات باید برای گرمایش، برای نیازهای آب گرم یا برای برگشت به دیگ ها بازیابی شود. آنها برای لوله کشی بخار، جداکننده ها و همه تجهیزات بخار گرم یا بخار کار می کنند.
- عایق لوله کشی: بیشتر سیستم های لوله کشی برای انتقال موادی استفاده می شود که در دمای بسیار بالاتر از دمای هوای اطراف قرار دارند. به عنوان مثال می توان به لوله کشی اصلی بخار و لوله کشی آب تغذیه اشاره کرد. به منظور کاهش مقدار حرارت از دست رفته به هوای اطراف از ماده داغ، لوله کشی با عایق پوشانده می شود. عایق نه تنها گرما را در خطوط گرم نگه می دارد، بلکه از بالا رفتن نامطلوب دمای داخل ساختمان کارخانه فرآیند نیز جلوگیری می کند. علاوه بر این، عایق بندی خطوط لوله داغ از آسیب دیدن پرسنل در اثر تماس با سطوح لخت لوله جلوگیری می کند. در مورد لوله کشی هایی که مواد را در دمای کمتری نسبت به هوای اطراف حمل می کنند، عایق کاری لوله از تعریق لوله و در نتیجه چکیدن و خوردگی لوله جلوگیری می کند.
یک ماده مناسب برای استفاده به عنوان عایق باید دارای ویژگی های زیر باشد.
- ارزش عایق بالا
- زندگی طولانی.
- اثبات حیوانات موذی
- غیر خورنده
- توانایی حفظ شکل و ارزش عایق در هنگام خیس شدن.
- سهولت کاربرد و نصب.
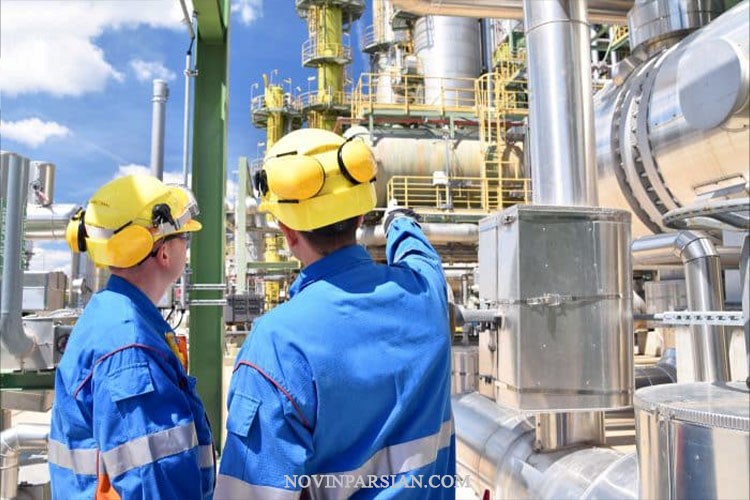
برخی از رایجترین مواد مورد استفاده برای عایقبندی لولهها در بخشهای زیر مورد بحث قرار میگیرند.
- سیلیس دیاتومه: این ماده با خاک رس و آزبست پیوند خورده است و برای دماهای تا 1030 درجه سانتیگراد استفاده می شود.
- آزبست: بخش های پوشش لوله از الیاف آزبست ساخته شده و برای دماهای تا 650 درجه سانتیگراد استفاده می شود.
- سیلیکات کلسیم: این عایق از سیلیس و آهک ساخته شده و برای دمای تا 650 درجه سانتی گراد مناسب است.
- شیشه سلولی: این ماده شیشه ای است که ذوب و کف شده و سپس به شکل های پوشش لوله قالب گیری شده است. برای دمای 430 درجه سانتیگراد قابل استفاده است.
- منیزیم (85%): این ماده از کربنات منیزیم با فیبر آزبست تشکیل شده است. به صورت قالبی برای پوشش لوله و همچنین به صورت پودری عرضه می شود تا با آب مخلوط شود و سیمان عایق تشکیل شود که برای پوشش اتصالات لوله استفاده می شود. پوشش لوله منیزیا برای سرویس دهی تا دمای 315 درجه سانتیگراد مناسب است.
- الیاف شیشه ای: شیشه ای است که به الیاف تبدیل شده و سپس به بخش های پوشش لوله تبدیل شده است که برای دماهای تا 190 درجه سانتیگراد مناسب است.
- فوم های پلاستیکی: اینها پلاستیک هایی هستند که در طول ساخت به فوم تبدیل شده و سپس به بخش های پوشش لوله تبدیل می شوند. آنها برای دماهای پایین -170 درجه سانتیگراد و تا 120 درجه سانتیگراد در دسترس هستند.
تجهیزات و ابزار پایپینگ
ابزارها اجزای حیاتی در سیستم های لوله کشی هستند زیرا برای اطمینان از جریان روان سیال و حفظ سطح تولید و کیفیت مطلوب مورد نیاز هستند. ابزارها پارامترهای فرآیند مانند دما، فشار، جریان و سطح را حس می کنند، انتقال می دهند، نشان می دهند، ثبت می کنند یا کنترل می کنند. یک ابزار باید تغییر در پارامتری مانند دما، فشار یا جریان را تشخیص دهد تا مفید باشد. این تغییر به سیگنالی مانند جریان یا ولتاژ تبدیل می شود که برای تفسیر کالیبره شده است. اغلب نیاز به تغییر سیگنال از یک شکل انرژی به شکل دیگر وجود دارد. به عنوان مثال، یک سیگنال جریان ممکن است باید به سیگنال فشار یا برعکس تبدیل شود. برای این کاربرد از مبدل استفاده می شود.
انواع رایج ابزار در سیستم لوله کشی آموزش پایپینگ شامل سنسورها، مبدل ها، آلارم ها، نشانگرها، ضبط کننده ها، رگولاتورها و کنترل کننده ها می باشد. ابزارها فقط پس از کالیبره شدن دقیق مفید هستند. رایجترین نوع کالیبراسیون، کالیبراسیون استاتیکی است که در آن مقادیر مقادیر فیزیکی در حین کالیبراسیون ثابت میمانند. فقط بزرگی متغیرهای ورودی و خروجی مهم است. گاهی اوقات کالیبراسیون دینامیکی ضروری است و از سیگنال های تست استاندارد مانند سیگنال های سینوسی یا پله ای استفاده می شود. دقت و دقت از ویژگی های دستگاه ایستا هستند که در کاربردهای آنها بسیار مهم است. سازندگان ابزار معمولاً دقت و دقت را به عنوان درصدی از دهانه خروجی ابزار بیان می کنند. ابزار دقیق پیکربندی یک ابزار یا گروهی از ابزار است که می تواند کنترل یک متغیر فرآیند را انجام دهد.
انواع ابزارهای فرآیندی
ابزار دستگاهی است که می تواند یک متغیر فرآیند را اندازه گیری، نمایش، نظارت و یا کنترل کند. اینها شامل متر و گیج (وسایل اندازه گیری یا حسگر)، دستگاه های نمایشگر، کنترل کننده ها، فرستنده ها و شیرها می باشد. یک ابزار اندازه گیری اندازه یک متغیر فرآیند را تعیین می کند. با توجه به عملکرد آنها، ابزارها ممکن است به عنوان سنسور، مبدل، فرستنده، کنترل کننده، تنظیم کننده، ضبط کننده، آلارم و نشانگر طبقه بندی شوند. سنسورها و فرستنده ها ابزار اندازه گیری رایج در سیستم های لوله کشی هستند.
حسگر
سنسورها اغلب مبدل های تقویت شده هستند. نمونه هایی از سنسورها ترموکوپل ها، فشار سنج ها، سطح سنج ها و فلومترها هستند. سنسورهای سطح الکترونیکی شامل خازن، سنسور اولتراسونیک و تشعشع هستند. دبی سنج های الکترونیکی شامل کنتورهای اولتراسونیک، توربین و الکترومغناطیسی می باشد. دستگاههای استرینگیج و پیزوالکتریک سنسور فشار الکترونیکی هستند. ترموکوپل ها، دستگاه های دمای مقاومتی (RTD) و ترمیستورها مبدل های حسگر دما الکترونیکی هستند. عنصر اولیه معمولا سیگنال خود را به فرستنده می فرستد.
مبدل
مبدل وسیله ای است که یک شکل انرژی را به دیگری تبدیل می کند. مبدل ها به طور گسترده در سیستم های کنترل استفاده می شوند و اغلب بخشی جدایی ناپذیر از سنسورها و فرستنده ها هستند. مبدل های معمولی مبدل های جریان پنوماتیک (P/I) یا جریان-پنوماتیک (I/P) و مبدل های فشار ولتاژ (E/P) هستند.
فرستنده
فرستنده ها دستگاه هایی هستند که یک متغیر فرآیند اندازه گیری شده را در محدوده سیگنال استاندارد قرار می دهند. سیگنال های رایج کنترل فشار، ولتاژ و جریان هستند. ضریب فشار استاندارد 3 تا 15 psig است. محدوده ولتاژ استاندارد 1 – 5 ولت DC است. و محدوده استاندارد جریان 4 تا 20 میلی آمپر DC است. فرستنده ها گاهی اوقات به عنوان مبدل عمل می کنند و سیگنال ها را به کنترل کننده ها، ضبط کننده ها، نشانگرها و آلارم ها ارسال می کنند.
کنترل کننده
کنترلر از سیگنال کنترل یا خطایی که دریافت می کند برای هدایت عنصر کنترلی یا تنظیم کننده نهایی استفاده می کند. این مغز یا تصمیم گیرنده در یک حلقه کنترل است. یک کنترل کننده دارای یک مقایسه کننده است، دستگاهی که مقدار خروجی یک فرآیند را با مقدار مرجع مقایسه می کند و یک سیگنال خطا تولید می کند. سیگنال خطا ممکن است یک سیگنال ولتاژ، جریان الکتریکی یا فشار هوا باشد. سیگنال خطا ممکن است قبل از اعمال به عنصر کنترل نهایی تقویت شود. کنترلرها دارای الگوریتم های داخلی هستند که اقدام اصلاحی مورد نیاز عنصر کنترل نهایی را تعیین می کنند.
رگولاتور
رگولاتور عنصر کنترل نهایی نیز نامیده می شود. از سیگنال کنترل از کنترل کننده برای تنظیم متغیر کنترل استفاده می کند تا سیگنال خطا را به حداقل برساند یا حذف کند. نمونه هایی از عناصر نهایی عبارتند از: شیرهای کنترل، درایوهای با سرعت متغیر، رله ها، پمپ ها و دمپرها. چندین ابزار ممکن است روی یک شاخه لوله نصب شود. ابزارهای نشان داده شده شامل دریچه های جریان، شیرهای فشار و گیج ها، دماسنج ها، نشانگرهای سطح و غیره است.
ابزار اندازه گیری
ابزارهای اندازه گیری با تشخیص تغییرات در سطوح، اندازه متغیرهای فرآیند را حس کرده و تعیین می کنند. آنها برای خواندن و ضبط کالیبره شده اند. ابزارهای اندازه گیری به شدت حواس انسان را گسترش می دهند و ممکن است به عنوان متر و سنج طبقه بندی شوند. گیج ها اغلب به فشارسنج و سطح سنج اشاره می کنند.
- اندازه گیری دما: دماسنج ها ممکن است به مقیاس های مختلف دما کالیبره شوند. سنسورهای دما بر این اساس کار می کنند که خواص خاصی از مواد به تغییرات دما پاسخ می دهند. دماسنج ها بر اساس انبساط و انقباض گازها، مایعات یا جامدات به دلیل تغییرات دما کالیبره می شوند. از این رو، دماسنج مایع، دماسنج گازی و دماسنج جامد (دو فلزی) وجود دارد. خواص الکتریکی و الکترونیکی نیز به تغییرات دما پاسخ می دهند که منجر به حسگرهای دما مانند ترموکوپل ها، آشکارسازهای دمای مقاومتی (RTD) و ترمیستورها می شود. سنسورهای دمایی مبتنی بر تابش حرارتی، پیرومتر نامیده می شوند.
- سنسورهای فشار: سنسورهای فشار رایج ترین ابزار در کارخانه های فرآیندی هستند. اندازه گیری دقیق فشار در کارخانه های صنعتی به دلیل انفجار احتمالی ناشی از فشار بالا بسیار مهم است. انفجار می تواند باعث آسیب به پرسنل یا آسیب رساندن به تجهیزات شود. اغلب دستگاه های تحت فشار در محدوده فشار کار می کنند و می توان آلارم ها را برای نشان دادن انحراف از محدوده تنظیم کرد. خاموش شدن تجهیزات ممکن است با انحراف از تنظیم محدوده فشار آغاز شود. یکی دیگر از دلایل اندازه گیری دقیق فشار این است که کیفیت یک محصول ممکن است گاهی تحت تأثیر فشار و دما باشد. به حداکثر رساندن کارایی و بهره وری فرآیندها اغلب نیاز به اطلاعات دقیق فشار دارد.
- سنسورهای فشار معمولاً فشار سنج نامیده می شوند. آنها را می توان به گیج های مایع، مکانیکی و الکتریکی طبقه بندی کرد. فشارسنج های مایع را مانومتر می نامند. گیج های فشار مکانیکی متداول شامل گیج های بوردون، بیلوز و دیافرام می باشد. گیج های فشار الکتریکی رایج عبارتند از: مقاومت، ظرفیت خازنی، اندوکتانس، رلوکتانس و سنسورهای پیزوالکتریک. گیج های فشار به تغییرات فشار اتمسفر محیط حساس هستند، به ویژه آنهایی که در فضاهای بسته قرار دارند. نصب صحیح باید انجام شود تا این اثر که باعث از بین رفتن دقت می شود به حداقل برسد. قابلیت اطمینان و دقت گیج های فشار نیز تحت تأثیر دمای محیط است. این به این دلیل است که مقاومت عناصر الکتریکی در
مدارهای ابزار دقیق ممکن است مستقیماً تحت تأثیر قرار گیرند. اثرات دما با طراحی مدار و نگهداری مناسب گیج که باید در محیط مناسب استفاده شود کاهش می یابد. بازرسی و کالیبراسیون مجدد باید در فواصل منظم انجام شود.
- فلومترها: فلومتر برای اندازه گیری دبی و یا سرعت سیال استفاده می شود. فلومتر معمولاً ترکیبی از مبدل، فرستنده و صفحه نمایش است. مبدل جریان را حس می کند، فرستنده متغیر جریان را به مقدار خروجی استاندارد می دهد و صفحه نمایش اندازه جریان را نشان می دهد. اغلب پانل اندازه گیری را نیز ثبت می کند. خدمات مختلف به انواع مختلفی از فلومترها نیاز دارند، بنابراین تعداد زیادی فلومتر برای نیازهای خاص طراحی شده اند. کنتورهایی وجود دارند که سرعت جریان را اندازه گیری می کنند که شامل دبی متر توربین، مغناطیسی، اولتراسونیک و گرداب می شود. دبی سنج های جابجایی مثبت دبی سیال را اندازه گیری می کنند و چندین مورد از آنها مانند دنده سنج ها وجود دارد. کوریولیس و متر حرارتی دبی جرمی هستند. دبی سنج های استنباطی آنهایی هستند که برای استنتاج سرعت یا سرعت جریان بر اساس اندازه گیری سایر متغیرها مانند فشار دیفرانسیل استفاده می شوند. در کنتورهای الکترونیکی، جریان از تغییرات یا اختلالات خواص الکتریکی یا الکترونیکی مواد حسگر در اثر جریان سیال تعیین می شود. اینها ممکن است خواص دما، مغناطیسی یا صدا باشند که می توانند به متغیرهای ولتاژ یا جریان تبدیل شوند. هنگام انتخاب فلومتر باید به دقت در مورد نوع جریان توجه شود. از آنجایی که نوع جریان توسط عدد رینولدز تعیین می شود، بر نوع فلومتر برای کاربردهای خاص تأثیر می گذارد زیرا فلومترها ممکن است برای جریان آرام یا آشفته طراحی شوند. فلومتر طراحی شده برای جریان آرام در صورت استفاده در یک خط جریان متلاطم، قرائت های اشتباهی را نشان می دهد. به طور مشابه، یک فلومتر طراحی شده برای جریان آشفته، در صورت استفاده در یک خط جریان آرام، قرائت های اشتباهی را نشان می دهد.
منابع:
https://learning.hccs.edu/faculty/edward.osakue/pdms/course-notes/Unit7-Piping%20Instruments1.pdfhttps://www.theprocesspiping.com/introduction-to-piping-system/