آشنایی با جوشکاری فلزات: اصول و مبانی آموزشی
مدیریت پروژه
یکی از دانش های اساسی که برای داشتن یک جوشکار ماهر لازم است، درک فلزات جوشکاری است. هر یک از فلزات و آلیاژهای فلزی به طور متفاوتی به گرما واکنش نشان می دهند و می توان به طور متفاوتی با آن ها کار کرد. وقتی فلزات گرم می شوند، منبسط می شوند و نرم تر می شوند و کاربردها و کاربردهای مختلفی را ایجاد می کنند. علاوه بر این، آنها به روش های مختلف جوشکاری که به کار می روند واکنش متفاوتی نشان می دهند. در این مطلب از آموزشگاه فنی به اساس جوشکاری انواع فلزات مناسب جوشکاری، چالش ها و بهترین تکنیک های جوشکاری آن ها می پردازیم.
انتخاب فلزات مناسب جوشکاری
جوشکاری به سادگی به عنوان فرآیند اتصال دو فلز از طریق عامل گرما یا فشار علاوه بر مواد فیلتر تعریف می شود. با این وجود، روش های جوشکاری زیادی برای انجام وظیفه در این تعریف ساده وجود دارد. علاوه بر این، به قطعاتی که به یکدیگر متصل می شوند، ماده اصلی یا ماده پایه و مواد اضافی برای تشکیل اتصال را پرکننده یا مصرفی می گویند. مواد مصرفی معمولاً به گونه ای انتخاب می شوند که از نظر ترکیب مشابه با تشکیل یک جوش همگن باشند. گرما به روش های مختلفی مانند قوس الکتریکی، قوس پلاسما و لیزر تامین می شود. جوش به عنوان یک اتصال جوشی تکمیل شده گفته می شود. قبل از داشتن اطلاعات بیشتر در مورد روش های جوشکاری، هنگام تصمیم گیری در مورد نوع روش های جوشکاری برای شرایط مورد نظر خود، مهم است که این عوامل زیر را در نظر بگیرید:
- سطح ذوب
- شکل پذیری فلز یا نحوه واکنش آن به خم شدن و کشش
- رسانایی الکتریکی فلز
- نقطه تسلیم فلز.
- نوع مواد قطعه کار
- ضخامت مواد
- موقعیت جوش
- زمان مورد نیاز
- نوع منبع جریان جوشکاری و مقدار جریان
جوشکاری فولاد
فولاد یک آلیاژ با 2٪ عناصر اضافی و آهن است. آلیاژهای ساخته شده از کربن و فولاد رایج هستند و در گریدهای بالا، پایین و متوسط وجود دارند. فولاد غنی از کربن قوی تر است. فولاد یک ماده انعطاف پذیر است که ممکن است با هر روشی جوش داده شود. لازم است اطراف جوش را تمیز کنید. اکسیداسیون می تواند باعث خوردگی و پوسته پوسته شدن آن شود.
روش های صحیح جوشکاری و اطمینان از مونتاژ صحیح تمامی قطعات فولادی و مطابقت با مشخصات مورد نظر مدیریت پروژه بسیار مهم است. در ساخت فولاد، مهمترین تکنیک های جوشکاری عبارتند از: جوشکاری با گاز بی اثر فلز (MIG)، جوشکاری با قوس تنگستن گازی (TIG) و جوش قوس فلزی محافظ.
- روش جوشکاری با گاز بی اثر فلز (MIG): جوشکاری با گاز بی اثر فلزات (MIG) به دلیل روش سریع و هزینه سرمایه گذاری اولیه کمتر از روش های دیگر جوشکاری پرکاربرد است. اجزای ضروری جوش MIG عبارتند از سیلندر گاز، رگلاتور، واحد تغذیه سیم، منبع تغذیه، مشعل MIG. برای یک جوش موفق، باید یک شیار جوش مناسب وجود داشته باشد که دهانه ای بین دو عضو مشترک باشد که فضایی را برای محتوی فلز جوش فراهم می کند. همچنین الکترود جوشکاری که تامین کننده جریان در این فرآیند است باید تمیز و عاری از روغن باشد. در روش MIG از یک الکترود جوش سیم استفاده می شود که به طور خودکار از طریق یک تفنگ جوش تغذیه می شود و این باعث ایجاد قوس بر روی قطعه کار می شود. قوس برای ذوب شدن مواد گرما تولید می کند. این مراحل تحت یک گاز بی اثر برای محافظت از جوش در برابر آلاینده ها در محیط جوش انجام می شود. انواع متداول گازی که برای این مورد استفاده می شود، آرگون، دی اکسید کربن و هلیوم هستند. فرآیند گاز بی اثر فلزی برای همجوشی فولاد نرم، فولاد کم کربن، فولاد ضد زنگ و آلومینیوم، فلزات مناسب جوشکاری صفحه نازک یا ضخیمتر مناسب است. برای کاربردهای اتصال دوره ای و معمولی، جوش MIG مزایای بیشتری نسبت به سایر فرآیندهای جوشکاری می دهد.
- روش قوس تنگستن گازی (TIG): جوشکاری قوسی تنگستن گاز یکی از رایجترین شکلهای جوشکاری است که در دهه 1930 توسعه یافت و در صنعت هواپیماسازی رایج بود. امروزه به طور کلی برای جوشکاری برنج، فولاد ضد زنگ، طلا، آلومینیوم، برنز و غیره استفاده می شود. ناحیه جوشکاری TIG از آلودگی اتمسفر توسط گاز بی اثر مانند جوشکاری MIG محافظت می کند، تفاوت اصلی بین این دو TIG از تنگستن استفاده می کند در حالی که MIG از الکترود استفاده می کند. در جوشکاری قوسی تنگستن گاز از یک الکترود تنگستن غیر قابل مصرف برای به دست آوردن جوش استفاده می شود. جریان های الکتریکی از طریق یک الکترود تنگستن کار می کنند و بنابراین گرما را برای ذوب شدن پایه مواد ایجاد می کنند و پس از آن یک قوس ایجاد می کنند که سیم را ذوب کرده و حوضچه جوش را ایجاد می کند. این فرآیند جوشکاری حرارت کم ایجاد می کند که آن را برای جوشکاری قطعات نازک مناسب تر می کند. این نوع جوش معمولاً برای فولاد آلیاژی، فولاد ضد زنگ، فلزات مناسب جوشکاری غیرآهنی مانند آلومینیوم، منیزیم و آلیاژهای مس استفاده می شود.
- روش استیک یا SWAW: جوشکاری قوس فلزی محافظ ، یک روش جوشکاری دستی قدیمی است. هنگامی که تجهیزات جدید و گرانتر در دسترس نیستند، این روش جوشکاری میتواند بسیار مفید باشد. این تکنیک دارای یک الکترود مصرفی با پوشش شار است که از ناپایدار شدن قوس به دلیل شرایط محیطی مانند هوا و باد جلوگیری می کند. این روش محدود به فلزات نازکتر از گیج 18 است و به دلیل حذف سرباره، نیاز به تمیز کردن ناحیه جوش دارد. این شرایط محدود کننده باعث میشود که این سبک جوشکاری برای علاقهمندان یا کارهای تعمیر و نگهداری کوچک مناسبتر باشد، زمانی که میتوان از روشهای جوشکاری دیگر در چندین صنعت برای اتصال قطعات استفاده کرد. برخلاف سایر روش های جوشکاری، گاز محافظ مورد نیاز نیست، در نتیجه مقرون به صرفه ترین روش است.

جوشکاری فولاد ضد زنگ
بر خلاف فولاد معمولی، فولاد ضد زنگ در برابر خوردگی مقاوم است. این امر از طریق افزودن کروم 10 تا 30 درصد به عناصر دیگر نظیر نیکل انجام می شود. برای جوشکاری فولاد ضد زنگ از جوش قوس الکتریکی (TIG، MIG یا Stick) استفاده می شود.
جوشکاری فولاد ضد زنگ، به ویژه، مجموعه ای از چالش های منحصر به فرد را در جوشکاری از نظر خواص مکانیکی آن ارائه می دهد. درجات و انواع مختلف آن (مانند آستنیتی، فریتی، دوبلکس و غیره) یک لایه پیچیدگی اضافی به موضوع می بخشد. جوشکاری فولاد ضد زنگ نیز عاری از مشکلات نیست در زیر به برخی از چالش های جوشکاری آن می پردازیم:
- تاب برداشتن و ترک خوردگی: فولاد ضد زنگ دارای رسانایی حرارتی کم و انبساط حرارتی بالا است که آن را مستعد تاب خوردگی و ترک خوردن می کند. گرمای بیش از حد ورودی در حین جوشکاری یا تغییر سریع دما، فلز را تحت فشار قرار می دهد و در نتیجه با سرد شدن اعوجاج ایجاد می کند. چند راه برای جلوگیری از تاب برداشتن و ترک خوردن وجود دارد که یکی از آنها کار با حرارت ورودی کمتر است. اگرچه ممکن است منطقی به نظر برسد، اما ممکن است به دلیل همجوشی ناقص بین قطعات کار منجر به کیفیت پایین جوش شود. بنابراین همیشه مهم است که بین این دو امر تعادل برقرار کنید. راه حل دیگر ایجاد هیت سینک با بستن مس یا برنج در پشت درز و جذب گرمای غیر ضروری به آلیاژهای مس است.
- زنگ زدگی: فولاد ضد زنگ به داشتن مقاومت در برابر خوردگی بالا شناخته شده است، با این حال گرمای بیش از حد ممکن است همچنان زنگ زدگی در جوش ایجاد کند. همچنین ممکن است از آنجایی که کربن حاصل از مواد پرکننده، ناحیه تحت تأثیر گرما را آلوده می کند، تشکیل شود. انتخاب دمای جوش بهینه و آلیاژ پرکننده فولاد ضد زنگ بسته به کار، خطر ایجاد زنگ زدگی در مواد را تا حد زیادی کاهش می دهد.
- جوشکاری فولادهای غیر مشابه: جوش زدن فلزات مناسب جوشکاری غیرمشابه یا انواع مختلف فولاد ضد زنگ با هم می تواند چالش برانگیز باشد، به خصوص اگر نقطه ذوب آنها از هم دور باشد. ممکن است در همجوشی موثر فلزات مشکل بزرگی ایجاد کند. انتخاب میله پرکننده بهینه هنگام جوشکاری فولاد ضد زنگ و آلیاژ دیگر ضروری است. پیش گرم کردن فلزات نیز می تواند این مشکل را کاهش دهد.
- دودهای سمی: جوش فولاد ضد زنگ دود سمی را به شکل گاز کروم شش ظرفیتی تولید می کند. زمانی که لایه اکسید کروم از بین میرود، ایجاد میشود و ممکن است در طی فرآیند گرمایش یا سرمایش رخ دهد. یک ماسک تنفسی موثر همراه با تهویه مناسب در ناحیه، کلید تضمین ایمنی جوشکار است.
جوشکاری آلومینیوم
مشابه فولاد ضد زنگ، آلومینیوم نیز نسبت به سایر فلزات مناسب جوشکاری کمتر خورنده است اما در مقایسه با فولاد ضد زنگ، سبک تر است. در جوشکاری از آلومینیوم خالص و آلیاژ های آن استفاده می شود. جوشکاری آلومینیوم به دلیل خواص مکانیکی منحصر به فرد آن در صنایع تولیدی و هوافضا بسیار رایج است. آلومینیوم سبک وزن، بادوام و کاملاً مقاوم در برابر خوردگی است که آن را به انتخابی جذاب برای برخی کاربردها در مقایسه با فلزات دیگر تبدیل می کند. با این حال، جوشکاری آلومینیوم برای دستیابی به نتیجه ای موفق و بدون نقص با مجموعه ای از چالش های منحصر به فرد مواجه است.
جوشکاری آلومینیوم فرآیند پیچیده ای است که نیازمند دانش، مهارت و تجربه است. درک فرآیندهای مختلف جوشکاری مناسب برای آلومینیوم و چالشها و راهحلهای مربوط به آن روشها برای دستیابی به اتصالات جوشکاری موفق بسیار مهم است. در ادامه به برخی از چالش های جوشکاری این فلز میپردازیم:
- اکسیداسیون: آلومینیوم وقتی در معرض جو قرار می گیرد به سرعت اکسید می شود و یک لایه اکسید نازک با دمای ذوب بالاتر (2072 درجه سانتیگراد) نسبت به آلومینیوم (660 درجه سانتیگراد) تشکیل می دهد. جوشکاری از طریق این مانع ممکن است قطعه کار را بسوزاند. لایه اکسید را می توان با استفاده از حلال ها یا اسیدها قبل از جوشکاری قطعه کار حل کرد. می توان آن را از طریق تکنیک های ساینده مکانیکی از طریق یک برس سیمی فولاد ضد زنگ انحصاری یا سندبلاست حذف کرد.
- تخلخل: آلومینیوم در حالت مذاب، مقادیر زیادی هیدروژن را جذب می کند و در نتیجه حفره های کوچک یا حباب هایی در فلز جوش ایجاد می شود. این یکپارچگی ساختاری فلز را ضعیف می کند و آن را در برابر شکست ناشی از فشار و تنش آسیب پذیر می کند. تخلخل با استفاده از مواد و تجهیزات تمیز، حذف روغن و گریس از سطح فلز و استفاده از گاز محافظ برای محدود کردن آلودگی به حداقل می رسد.
- ناخالصی ها: روغن، خاک، هوا و ذرات می توانند بر ناحیه جوش تأثیر منفی بگذارند و بر استحکام و ظاهر قطعه کار تأثیر بگذارند. این ناخالصی ها می توانند از منابع متعددی مانند محیط، تجهیزات، آماده سازی و ذخیره سازی به دست آیند. تغییر رنگ، دانه بندی، خوردگی و اکسید شدن نشانه هایی از ناخالصی در اتصال جوش را نشان می دهد. ذخیره سازی مناسب، نگهداری تجهیزات و آماده سازی فلز مراحلی است که باید برای جلوگیری از ناخالصی ها انجام داد.
- ضخامت: کار با آلومینیوم معمولاً شامل جوشکاری مواد با ضخامت های متفاوت است. جوشکاری از طریق ترکیبی از مواد نازک و ضخیم به طور همزمان می تواند مشکل باشد. گرمای اعمال شده بر روی قطعه کار ممکن است از طریق مواد نازک ذوب شود یا به اندازه کافی به مواد ضخیم نفوذ نکند تا یک اتصال جوش قوی ایجاد کند.
- ترک داغ: سطوح بالای تنش حرارتی می تواند منجر به ترک داغ یا ترک انجماد در جوش های آلومینیوم شود. این یکی از دلایلی است که آلومینیوم را برای جوشکاری قوس الکتریکی نامناسب می دانستند. ترکیب عناصر آلیاژی مختلف و پردازش آلیاژهای آلومینیوم می تواند خواص مکانیکی آن را به شدت بهبود بخشد. سری های درجه (Al-Cu) 2xxx و (Al-Zn) 7xxx آلیاژهای آلومینیومی هستند که قابلیت عملیات حرارتی دارند.
- رسانایی گرمایی: رسانایی حرارتی بالای آلومینیوم، نفوذ موفقیت آمیز در اتصال جوش را چالش برانگیز می کند، زیرا گرما را به سرعت جذب و دفع می کند. تنظیم تجهیزات جوشکاری برای گرمای ورودی بالاتر، نفوذ را بهبود می بخشد.
درک کامل درجات، روشها و تکنیکهای جوشکاری آلومینیوم، کلید موفقیت در جوشکاری موثر ضخامتهای مختلف ورق آلومینیوم است. جوشکارها می توانند با تنظیم پارامترهایی مانند آمپر و حرارت ورودی در سطوح بهینه، این فلزات مناسب جوشکاری را به طور موثر جوش دهند. روش ترجیحی برای جوشکاری آلومینیوم، جوشکاری TIG (GTAW) است. علاوه بر این، GMAW و سایر تکنیک های جوشکاری (جوشکاری قوس فلزی با گاز یا Mig) استفاده می شود. جوشکاری گاز محافظ فقط برای کارهای معمولی استفاده می شود. انتخاب طرح اتصال فلزی پایه (سه راهی، لبه یا گوشه) اولین گام در این روش است.
جوشکاری مس
مس به دلیل رسانایی الکتریکی، هدایت حرارتی، مقاومت در برابر خوردگی، زیبایی و مقاومت در برابر سایش، یک از فلزات مناسب جوشکاری مورد استفاده در صنعت و در نتیجه جوشکاری است. تکنیک های جوشکاری شامل لحیم کاری، لحیم کاری و جوشکاری است.
برای جوشکاری مس از جوشکاری قوس فلزی گازی و قوس الکتریکی تنگستن گازی استفاده می شود. جوشکاری قوس فلزی دستی تکنیکی است که توسط برخی از جوشکاران استفاده می شود. طرح های اتصالات برای جوشکاری مس عریض تر از طرح های توصیه شده برای فولاد است. آرگون به عنوان گاز محافظ مس استفاده می شود. برای تمیز کردن و چربی زدایی محل های جوش از برس سیمی برنز استفاده می شود. پس از جوشکاری، اکسیدهای تشکیل شده باید تمیز شوند. اگرچه مس از قبل گرم می شود، آلیاژهای مس به دلیل رسانایی حرارتی عالی نیازی به پیش گرم شدن ندارند.
هنگامی که مس با سایر آلیاژها و عناصر ترکیب می شود، قوی تر می شود و آن را برای مصارف صنعتی جذاب تر می کند. با افزودن عناصر دیگر، می توان آن را راحت تر ماشین کاری کرد و همچنین در برابر خوردگی مقاوم تر میشود. این آلیاژها می توانند شامل برنج و نیکل ، روی، قلع، آلومینیوم و سیلیکون باشند.
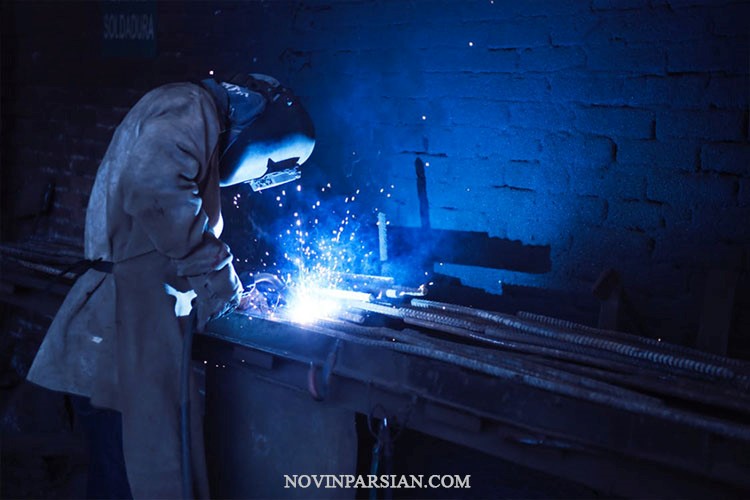
تکنیک های جوشکاری مس
متداول ترین تکنیک های جوشکاری مس عبارتند از جوشکاری با قوس فلزی گازی یا MIG، جوشکاری با قوس فلزی دستی و جوشکاری با قوس تنگستن گازی. مانند تمام تکنیک های آموزش جوشکاری، حفظ سرعت یکنواخت در طول فرآیند درز بسیار مهم است و میله پرکننده باید در حوضچه مذاب نگه داشته شود. این امر تضمین می کند که میله می تواند سطح نفوذ ثابتی را برای قوی ترین جوش ممکن حفظ کند.
جوشکاری قوس فلزی گاز برای مس از الکترودها استفاده می کند و به طور خودکار سیم و گازهای محافظ را به تفنگ جوش تغذیه می کند. جوشکاری قوس فلزی دستی برای انجام تعمیرات روی مس یا آلیاژهای مس استفاده می شود. همچنین به یک فلز پرکننده با بافت باریک نیاز دارد و به طور معمول از یک الکترود جریان مستقیم مثبت با تکنیک مهره رشته ای استفاده می کند.
جوشکاری قوسی تنگستن گازی مشابه بیشتر فرآیندهای جوشکاری قوس الکتریکی است اما از قوس الکتریکی برای گرم کردن و ذوب مس و مواد پرکننده استفاده میکند. با این حال، کمی متفاوت از تکنیک های دیگر است، زیرا از الکترود مصرفی برای انتقال برق به جوش قوس الکتریکی استفاده نمی کند. به همین دلیل، می تواند یک اتصال جوش با یا بدون مواد پرکننده ایجاد کند.
جوشکاری چدن
در مورد فلزات مناسب جوشکاری جوشکاری چدن نسبت به فولاد کم کربن نسبتا سخت تر است. چدن انعطاف پذیری کمتری دارد و سیلیکون و کربن بیشتری دارد. برای رهایی از هر گونه چربی و روغن جاسازی شده قبل از جوشکاری چدن، سطح را تمیز کنید. لازم است تمام ترک ها را سمباده بکشید. برای اتصال قطعات چدن از جوش اکسی استیلن استفاده می شود.
در بیشتر موارد، جوشکاری روی چدن شامل تعمیر قطعات ریختهگری میشود. تعمیرات ممکن است در ریخته گری که در آن قطعات ریخته گری تولید می شود انجام شود، یا ممکن است برای تعمیر عیوب ریخته گری که پس از ماشینکاری قطعه کشف می شود، انجام شود. قطعات چدنی که به اشتباه تراشیده شده است ممکن است نیاز به تعمیر توسط جوشکاری داشته باشند، مانند زمانی که سوراخ ها در محل نامناسب تعبیه می شوند. اغلب قطعات چدن شکسته با جوشکاری تعمیر می شوند. قطعات چدن شکسته با توجه به ماهیت شکننده اکثر چدن ها غیرعادی نیستند. در حالی که انواع مختلفی از چدن وجود دارد، رایج ترین آنها چدن خاکستری است.
چالش های جوشکاری جدن
چدن معمولاً دارای محتوای کربن 2٪ – 4٪ است، که تقریباً 10 برابر بیشتر از فولادها است. محتوای کربن بالا باعث می شود کربن به صورت تکه های گرافیت بسازد. این گرافیت به چدن خاکستری ظاهر مشخص خود را در هنگام شکستگی می دهد.
هنگام ریخته گری، آهن مذاب را در قالب ریخته و اجازه می دهیم به آرامی خنک شود. هنگامی که این ماده با کربن بالا به آرامی خنک شود، می توان ریخته گری بدون ترک ایجاد کرد. یادآوری این نکته هنگام جوشکاری چدن مفید است که در حین و بعد از جوشکاری، ریخته گری یا باید به آرامی خنک شود یا باید آنقدر خنک نگه داشته شود که سرعت خنک شدن آن مهم نباشد.
دمای بحرانی در اکثر چدن ها حدود 1450 درجه فارنهایت است. در این دما، شرایطی که می تواند منجر به ترک شود رخ می دهد. در حالی که قوس، ریخته گری را تا دمای بالاتر از این سطح گرم می کند، مهم است که ریخته گری برای مدت طولانی در این دما نگه داشته نشود.
تکنیک های جوشکاری چدن
- انتخاب الکترود: اگر قرار باشد قطعه بعد از جوشکاری ماشین کاری شود، یک الکترود نیکل مورد نیاز است. از الکترود Tech-Rod® 99 برای جوش های تک پاس استفاده میشود. Tech-Rod® 55 برای جوش های چند پاس ترجیح داده می شود. گاهی اوقات، پاسهای ریشه با Tech-Rod 99 وارد میشوند و به دنبال آن پاسهای پر با Tech-Rod 55 قرار میگیرند. برای جوشهایی که نیازی به ماشینکاری نیست و انتظار میرود که جوش مانند چدن زنگ بزند، الکترود Lincoln Ferroweld® میتواند مورد استفاده قرار گیرد.
- پیش گرمایش: به طور کلی، جوشکاری چدن با پیش گرمایش ترجیح داده می شود. اما، راه دیگر برای جوشکاری موفقیت آمیز چدن، خنک نگه داشتن آن است. در زیر هر دو روش توضیح داده خواهد شد. با این حال، هنگامی که یک روش را انتخاب کردید، به آن پایبند باشید.
- تکنیک جوشکاری با پیش گرم: پیش گرم کردن چدن قبل از جوشکاری سرعت خنک شدن جوش را کاهش می دهد و ناحیه اطراف جوش را احاطه می کند. در صورت امکان، همیشه ترجیح داده می شود که کل ریخته گری گرم شود. دمای پیش گرم معمولی 500-1200 درجه فارنهایت است. بیش از 1400 درجه فارنهایت گرم نکنید زیرا این باعث می شود که مواد در محدوده دمایی بحرانی قرار گیرند. قسمت جوش را به آرامی و یکنواخت از قبل گرم کنید. برای به حداقل رساندن اختلاط و تنش های پسماند، با استفاده از جریان کم جوش دهید. در برخی موارد، ممکن است لازم باشد که جوشها را به بخشهای کوچک و تقریباً 1 اینچی محدود کنیم تا از ایجاد تنشهای پسماند که میتواند منجر به ترک شود، جلوگیری شود. کندن مهره های جوش نیز در این زمینه می تواند مفید باشد. پس از جوشکاری، اجازه دهید قطعه به آرامی خنک شود. پیچاندن قالب در یک پتوی عایق، یا دفن آن در ماسه خشک، به کاهش سرعت خنک شدن و کاهش تمایل به ترک کمک می کند.
- تکنیک جوشکاری بدون پیش گرم: اندازه ریختهگری یا شرایط دیگر ممکن است نیاز داشته باشد که جوشکاری بدون پیش گرمایش انجام شود. در این حالت، قطعه باید خنک و نه سرد نگه داشته شود. افزایش دمای ریخته گری تا 100 درجه فارنهایت مفید است. هرگز قالب ریخته گری را چنان داغ نکنید که نتوانید دست خود را روی آن قرار دهید.
- جوش های کوتاه و تقریباً 1 اینچی: در این تکنیک، مهم است که قطعه جوش بعد از جوشکاری پوسته شود. اجازه دهید جوش و ریخته گری کاملا خنک شود. سرعت خنک شدن را با آب یا هوای فشرده تسریع نکنید. ممکن است امکان جوشکاری در ناحیه دیگری از ریخته گری در حالی که جوش قبلی سرد می شود وجود داشته باشد. تمام دهانه ها باید پر شوند. در صورت امکان، مهره ها باید در یک جهت قرار گیرند و ترجیح داده می شود که انتهای مهره های موازی با یکدیگر هم راستا نشوند.
- آب بندی ترک ها: حتی زمانی که رویههای خوبی دنبال میشوند، به دلیل ماهیت چدن، ترکهای ریز در کنار جوش ظاهر میشوند. اگر ریخته گری ضد آب مد نظر باشد، این امر می تواند مشکل ساز باشد. با این حال، نشت را معمولاً می توان با نوعی ترکیب آب بندی از بین برد در غیر این صورت پس از بازگشت به سرویس، خیلی زود زنگ خواهد زد.
- روش استادینگ: یکی از روشهایی که برای تعمیر شکستگیهای بزرگ در ریختهگریهای بزرگ استفاده میشود، ایجاد سوراخ روی سطوحی است که برای دریافت فلز جوش تعمیری اریب شدهاند. گل میخ های فولادی را در سوراخ های رزوه دار بپیچانید و 3/16 اینچ (5 میلی متر) تا ¼ اینچ (6 میلی متر) گل میخ را بالای سطح بگذارید. با استفاده از روشهایی که در بالا توضیح داده شد، ناودانیها را در جای خود جوش دهید و تمام سطح شکستگی را با رسوب جوش بپوشانید. هنگامی که یک رسوب جوش خوب ایجاد شد، دو طرف ترک را می توان به هم جوش داد.
منابع: